A trade lane (or trade route) refers to a specific pathway along which goods are transported between two or more locations, typically across international borders. Trade lanes are established based on the flow of goods and the economic relationships between countries or regions. They encompass both maritime and air routes and play a crucial role in global supply chains by facilitating the movement of goods and fostering international trade.
Transit time refers to the duration it takes for goods or shipments to travel from their origin to their destination. It is a crucial metric in supply chain and logistics management, as it directly impacts delivery schedules, inventory levels, and customer satisfaction. Transit time encompasses the entire journey of a shipment, including transportation, handling, and processing at various checkpoints along the route.
Transloading refers to the process of transferring goods or cargo from one mode of transportation to another, typically from one type of truck or railcar to another, or from rail to truck and vice versa. This logistical practice is often employed to optimize transportation routes, reduce costs, and improve overall efficiency in supply chain operations.
A Transportation Management System (TMS) is a specialized software solution designed to streamline and optimize transportation and logistics operations within supply chains. It provides functionalities to effectively manage and control the movement of goods from origin to destination.
Transportation lead time refers to the duration it takes for goods to be transported from the point of origin to the final destination. It encompasses the time required for transportation activities, including loading, transit, and unloading, across various modes of transport such as road, rail, air, or sea.
A transshipment is the process of transferring goods from one transportation vehicle or vessel to another during their journey from origin to destination. It typically occurs at intermediary points along the supply chain route, where cargo is transferred between different modes of transportation, carriers or vessels.
Twenty-foot Equivalent Unit (TEU) is a standard unit of measurement used in the shipping industry to quantify the cargo-carrying capacity of container vessels. It represents the volume of a standard twenty-foot-long shipping container.
An Ultra Large Container Vessel (ULCV) is a massive container ship used on major trade routes, capable of carrying over 14,000 TEUs.
Vendor Managed Inventory (VMI) is a supply chain management strategy where the supplier or vendor takes responsibility for managing the inventory levels of their products at the customer's or retailer's location. In this arrangement, the vendor monitors the inventory levels based on agreed-upon criteria such as sales data or inventory levels, and initiates replenishment as needed.
Verified Gross Mass (VGM) is a term used in the shipping industry to refer to the total weight of a packed container, including its contents and packaging materials. It is a crucial requirement mandated by the International Maritime Organization (IMO) under the Safety of Life at Sea (SOLAS) convention to enhance safety in maritime transportation.
A floating structure with its own mode of propulsion designed for the transport of cargo and/or passengers. In the Industry Blueprint 1.0 "Vessel" is used synonymously with "Container vessel", hence a vessel with the primary function of transporting containers.
A vessel sharing agreement (VSA) is a cooperative arrangement between shipping companies that allows them to share space and resources on vessels for specific routes.
Vessel bunching refers to the situation where multiple vessels arrive at a port simultaneously or within a short period, leading to congestion and delays. This clustering of vessels can overwhelm port facilities, causing extended wait times for berthing, loading, and unloading operations.
A vessel call sign is a unique identifier assigned to a ship for radio communication purposes. It is used to distinguish the vessel from others in maritime communication systems, including VHF radios and satellite communications.
A vessel omission (sometimes called a port omission) occurs when a scheduled vessel does not call at a planned port during its voyage. This disruption means that the vessel skips the port entirely, which can impact the transportation and delivery schedules of goods.
In cargo shipping, vessel rotation is the planned sequence of port calls that a shipping vessel follows on its route to optimize cargo loading and unloading operations.
The timetable of departure and arrival times for each port call on the rotation of the vessel in question.
A journey by sea from one port or country to another one or, in case of a round trip, to the same port.
Warehouse utilization is a logistics metric that refers to the effective use of available warehouse space for storing goods and inventory.
Order for specific transportation work carried out by a third party provider on behalf of the issuing party.
Logistics yard management refers to the process of overseeing and controlling the movement of trucks, trailers, containers, and other vehicles within a yard or distribution center. This includes tasks such as scheduling, tracking, and coordinating the arrival, departure, and storage of these vehicles.
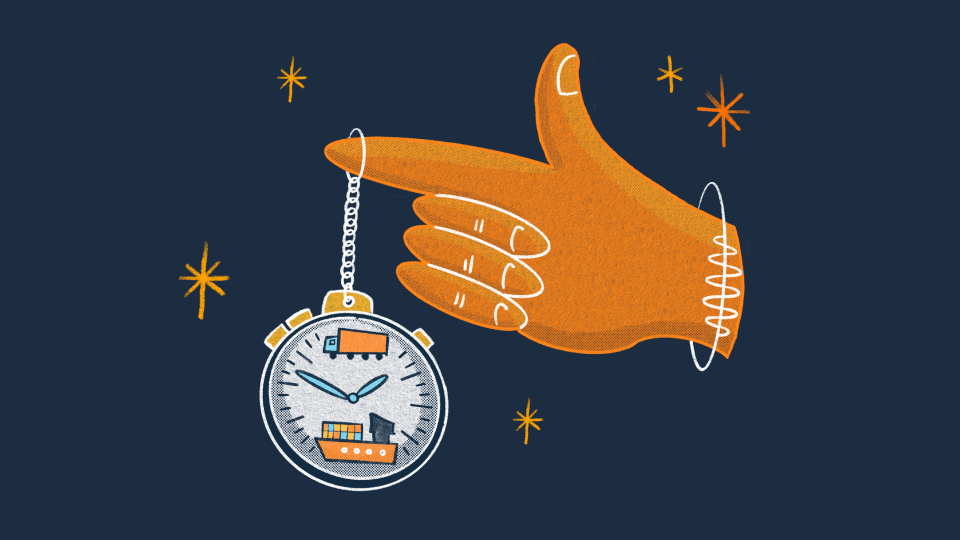
Make OTIF and perfect orders standard
If it’s not early, it’s late. Next-day delivery promises have changed the way we buy, setting expectations for every purchase to turn up when we want it, exactly as we ordered it. Whether you operate in a B2B or B2C context, the ‘Amazon effect’ has trickled through to shape expectations in every area of logistics and transportation.
Businesses are now just as demanding as end-consumers, so if you’re not taking steps to keep your own deliveries up to standard, then you risk tarnishing your reputation, incurring steep fines and losing customers.
For businesses to keep up with modern standards, they need to be investing in top-tier supply chain tracking, analytics, and visibility software, as well as the collaboration necessary to ensure smooth, timely handovers between all the different actors along the supply chain.
What is OTIF in supply chains and how can you achieve it?
We all know that OTIF means delivery on time and in full. But we also know there are thousands of different ways for a shipment to be delayed or disrupted – making OTIF much harder to achieve than the simple acronym suggests.
As far as the data is concerned though, OTIF is a strict, black-and-white assessment. If a delivery arrives after its scheduled time, it’s late. If the order isn’t right, has too few (or too many) items, or is damaged, then it hasn’t been fulfilled in full.
On the other side of the coin, if you are regularly achieving OTIF delivery, then you’re a lot closer to a crucial ‘perfect order’. A perfect order isn’t just received on time and in full, but also ticks all the right boxes around accurate documentation, labeling, and invoicing. The more of them you have, the more likely it is that you’re not just meeting customer expectations, but exceeding them.
Luckily, all of this is quite easy to measure, as long as you’re collecting the right data.
How to calculate OTIF performance
Assuming your packaging and documentation processes are up to scratch, the on-time delivery (OTD) part of OTIF is usually where perfect orders fall through. You can work this out as a percentage by comparing which of your orders arrived on time to those that didn’t, which is a handy way to see how much work you have to do.
Simply divide your number of your late orders by the total number of orders. That will give a percentage for how many orders were late, which you can use to work out how many achieved an OTD.
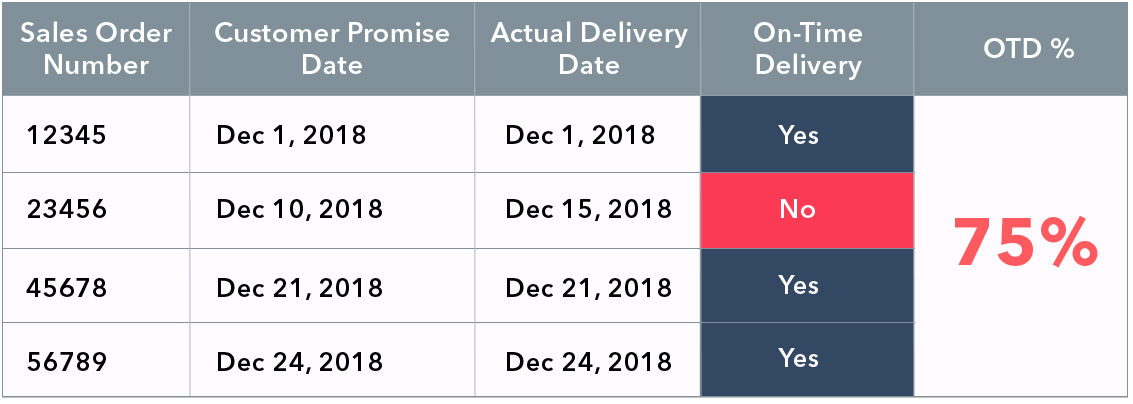
Why is on-time delivery so important as a business?
In the consumer world, late deliveries are a source of frustration that can lead to dissatisfied customers and reduced loyalty – along with reputational damage if they’re frequent enough to become the norm rather than the exception.
All of that is equally true for businesses that ship goods and materials to other businesses. If your organization gains a reputation for failing to deliver at OTIF or perfect order standards, then it should be no surprise when some of your customers start to look for more reliable alternatives.
The frustration can even seep into other parts of your supply chain, leading to disengaged employees, embarrassed partners, and stakeholders whose expectations are consistently being undermined. None of which is good for business.
Last, but certainly not least, there are very real financial consequences to missing on-time delivery. These can be broken down into three separate areas.
Firstly, there are the direct fines levied by customers towards wholesalers as a result of any late arrivals. These include chargebacks and OTIF fines, and are a clear sign of dissatisfaction as well as a financial penalty.
Then there’s the cost of empty shelves, which only means one thing if you’re a retailer – missed sales. No matter what you’re selling, if there’s no stock, there’s no revenue.
Finally, if your deliveries are arriving to customers late, it’s very likely that you’ll be incurring some sort of penalty, somewhere along the way. That could be demurrage fees, detention charges, or a host of other unnecessary costs that every business is better off without.
Visibility and the power to improve OTIF performance
You can’t regularly achieve OTIF deliveries without a thorough understanding of all the different factors that affect it. For that reason, better supply chain visibility should be your first port of call.
With a tool like Beacon that gives you a single source of truth for all of your shipping and transportation data, you’ll be able to easily see detailed reports of where delays are happening, what’s causing them, and from there, take appropriate action.
Delays could be occurring amongst your carriers, in your distribution centers, or at critical hand-off points between partners. But wherever they’re happening, you won’t be able to address them if you don’t have the supply chain data to know what’s going on.
Just as importantly, up-to-date data can be shared with your supply chain partners. Collaboration is the key to minimizing delays, because if everybody’s singing from the same songbook, it’s far less likely that small delays will be compounded by confusion and spiral into significant ones that dent your OTIF performance.
So if you want to get better visibility into your delays and access the collaborative tools that will help you eliminate them, invest in a real-time data solution that increases customer satisfaction, boosts loyalty, and helps you avoid unnecessary penalty fees.