A trade lane (or trade route) refers to a specific pathway along which goods are transported between two or more locations, typically across international borders. Trade lanes are established based on the flow of goods and the economic relationships between countries or regions. They encompass both maritime and air routes and play a crucial role in global supply chains by facilitating the movement of goods and fostering international trade.
Transit time refers to the duration it takes for goods or shipments to travel from their origin to their destination. It is a crucial metric in supply chain and logistics management, as it directly impacts delivery schedules, inventory levels, and customer satisfaction. Transit time encompasses the entire journey of a shipment, including transportation, handling, and processing at various checkpoints along the route.
Transloading refers to the process of transferring goods or cargo from one mode of transportation to another, typically from one type of truck or railcar to another, or from rail to truck and vice versa. This logistical practice is often employed to optimize transportation routes, reduce costs, and improve overall efficiency in supply chain operations.
A Transportation Management System (TMS) is a specialized software solution designed to streamline and optimize transportation and logistics operations within supply chains. It provides functionalities to effectively manage and control the movement of goods from origin to destination.
Transportation lead time refers to the duration it takes for goods to be transported from the point of origin to the final destination. It encompasses the time required for transportation activities, including loading, transit, and unloading, across various modes of transport such as road, rail, air, or sea.
A transshipment is the process of transferring goods from one transportation vehicle or vessel to another during their journey from origin to destination. It typically occurs at intermediary points along the supply chain route, where cargo is transferred between different modes of transportation, carriers or vessels.
Twenty-foot Equivalent Unit (TEU) is a standard unit of measurement used in the shipping industry to quantify the cargo-carrying capacity of container vessels. It represents the volume of a standard twenty-foot-long shipping container.
An Ultra Large Container Vessel (ULCV) is a massive container ship used on major trade routes, capable of carrying over 14,000 TEUs.
Vendor Managed Inventory (VMI) is a supply chain management strategy where the supplier or vendor takes responsibility for managing the inventory levels of their products at the customer's or retailer's location. In this arrangement, the vendor monitors the inventory levels based on agreed-upon criteria such as sales data or inventory levels, and initiates replenishment as needed.
Verified Gross Mass (VGM) is a term used in the shipping industry to refer to the total weight of a packed container, including its contents and packaging materials. It is a crucial requirement mandated by the International Maritime Organization (IMO) under the Safety of Life at Sea (SOLAS) convention to enhance safety in maritime transportation.
A floating structure with its own mode of propulsion designed for the transport of cargo and/or passengers. In the Industry Blueprint 1.0 "Vessel" is used synonymously with "Container vessel", hence a vessel with the primary function of transporting containers.
A vessel sharing agreement (VSA) is a cooperative arrangement between shipping companies that allows them to share space and resources on vessels for specific routes.
Vessel bunching refers to the situation where multiple vessels arrive at a port simultaneously or within a short period, leading to congestion and delays. This clustering of vessels can overwhelm port facilities, causing extended wait times for berthing, loading, and unloading operations.
A vessel call sign is a unique identifier assigned to a ship for radio communication purposes. It is used to distinguish the vessel from others in maritime communication systems, including VHF radios and satellite communications.
A vessel omission (sometimes called a port omission) occurs when a scheduled vessel does not call at a planned port during its voyage. This disruption means that the vessel skips the port entirely, which can impact the transportation and delivery schedules of goods.
In cargo shipping, vessel rotation is the planned sequence of port calls that a shipping vessel follows on its route to optimize cargo loading and unloading operations.
The timetable of departure and arrival times for each port call on the rotation of the vessel in question.
A journey by sea from one port or country to another one or, in case of a round trip, to the same port.
Warehouse utilization is a logistics metric that refers to the effective use of available warehouse space for storing goods and inventory.
Order for specific transportation work carried out by a third party provider on behalf of the issuing party.
Logistics yard management refers to the process of overseeing and controlling the movement of trucks, trailers, containers, and other vehicles within a yard or distribution center. This includes tasks such as scheduling, tracking, and coordinating the arrival, departure, and storage of these vehicles.
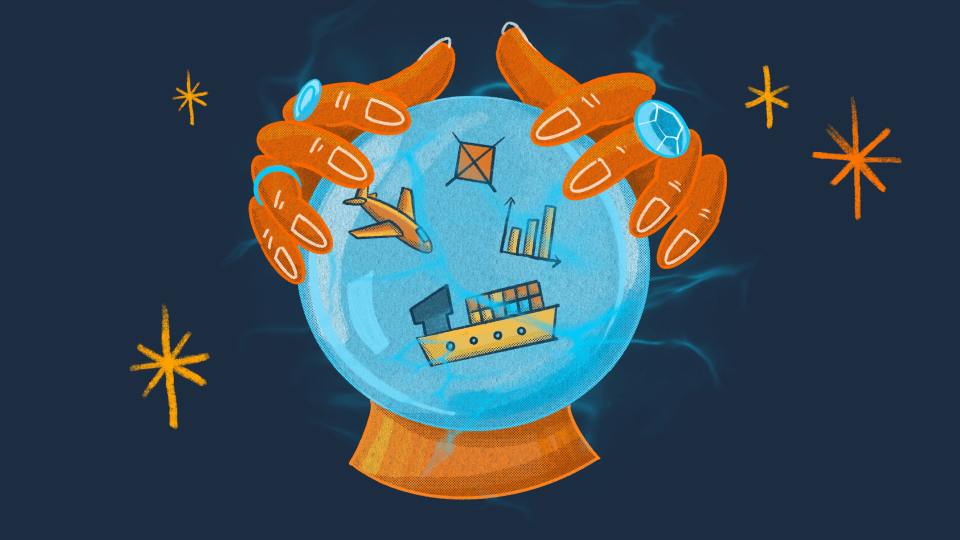
Risk management in supply chains: What you need to know to protect your inventory
There’s no getting around risk. It’s nothing new in global supply chains, and only getting more complex and harder to predict.
Today’s supply chains are particularly vulnerable to labor strikes, port congestion, geopolitical disruption, and supplier delays or bankruptcy – many of which are becoming more common. That creates enormous potential for destabilization, and makes risk management an absolute necessity.
A big part of the supply chain risk management challenge boils down to the presence of a wide range of actors needing to work in concert to effectively mitigate risks.
When something goes wrong, there’s often a chain reaction where disruption at one point leads to knock-on impacts at all the stages that follow.
Without quick and effective collaboration, it can be difficult, if not impossible, for partners at those later stages to know what’s happened and take the necessary action.
That’s why mitigation is the magic word in supply chain risk management. Anything that you can do to limit the consequences of a risk event is essential.
In supply chain risk management, visibility is control
If you want to control your supply chain and manage risk, then the first and most important thing you’ll need is supply chain visibility.
Supply chain visibility is an organization’s ability to see and understand the movement of goods and materials from place to place – and then share or analyze that data to gain a deeper understanding of supply chain performance and pinpoint problem areas.
Without a good visibility infrastructure, risk management is challenging because you won’t have the data or analytics to understand the persistent sources of risk or measure the impact of changes.
However, gaining this high level of visibility is difficult for businesses that lack the appropriate tools and processes.
Modern supply chains are complex, with multiple layers and countless partners involved. Relying on basic tools like carrier tracking portals might provide some of the data you need, but they’re not catch-all solutions.
You won’t be able to see all of your shipments in one place, and even if you do move the data into a centralized spreadsheet, there’s no easy way to keep it up to date without heavy manual processes.
Plus, these systems don’t allow you to share information across the supply chain, which is one of the key ways to reduce chain reaction impacts by ensuring partners and stakeholders are aware of issues and can react quickly and effectively.
Luckily, technology has opened the door to new, powerful visibility solutions that help mitigate risk.
By investing in and embracing innovative supply chain visibility platforms like Beacon, you get the visibility you need to not only better understand your supply chain, but protect against the risk within it too.
Here’s how.
Step 1: Get the supply chain visibility you need
For many businesses, the first step in risk reduction is to boost inventory levels.
This might insulate you from some of the consequences of supply chain disruption, but it’s far from a truly effective solution. Inventory is expensive.
It ties up a significant portion of your cash flow, can come with excessive carrying costs, and simply isn’t scalable as a long-term solution.
A more sustainable approach involves using supply chain visibility tools (like Beacon), to get a clear and deep understanding of your supply chain.
Having all your data in one place will make it easy to illuminate key drivers of risk and implement risk controls in steps 2 and 3.
Step 2: Identify your critical risk areas
A supply chain visibility tool with dedicated reporting features will give you detailed breakdowns of how your supply chain is performing across carriers, ports, routes, and other dimensions with all of that data held in one place for easy oversight.
With a single source of truth like Beacon, it’s far easier to determine which specific routes, ports, carriers, and even times of the year come with a higher chance of disruption.
For example, if there’s a particular route or carrier that’s consistently causing delays to your shipments (or to others), then you can start looking into alternatives or adjust lead times to better reflect reality.
Step 3: Build a supply chain risk management framework
Once you have better visibility into your supply chain and a clear breakdown of the risks that could disrupt it, you can start mapping them into a comprehensive risk management framework.
This might start as a list of areas with enhanced risk, broken down by the part of the supply chain they affect, as shown in the example from McKinsey & Company below.
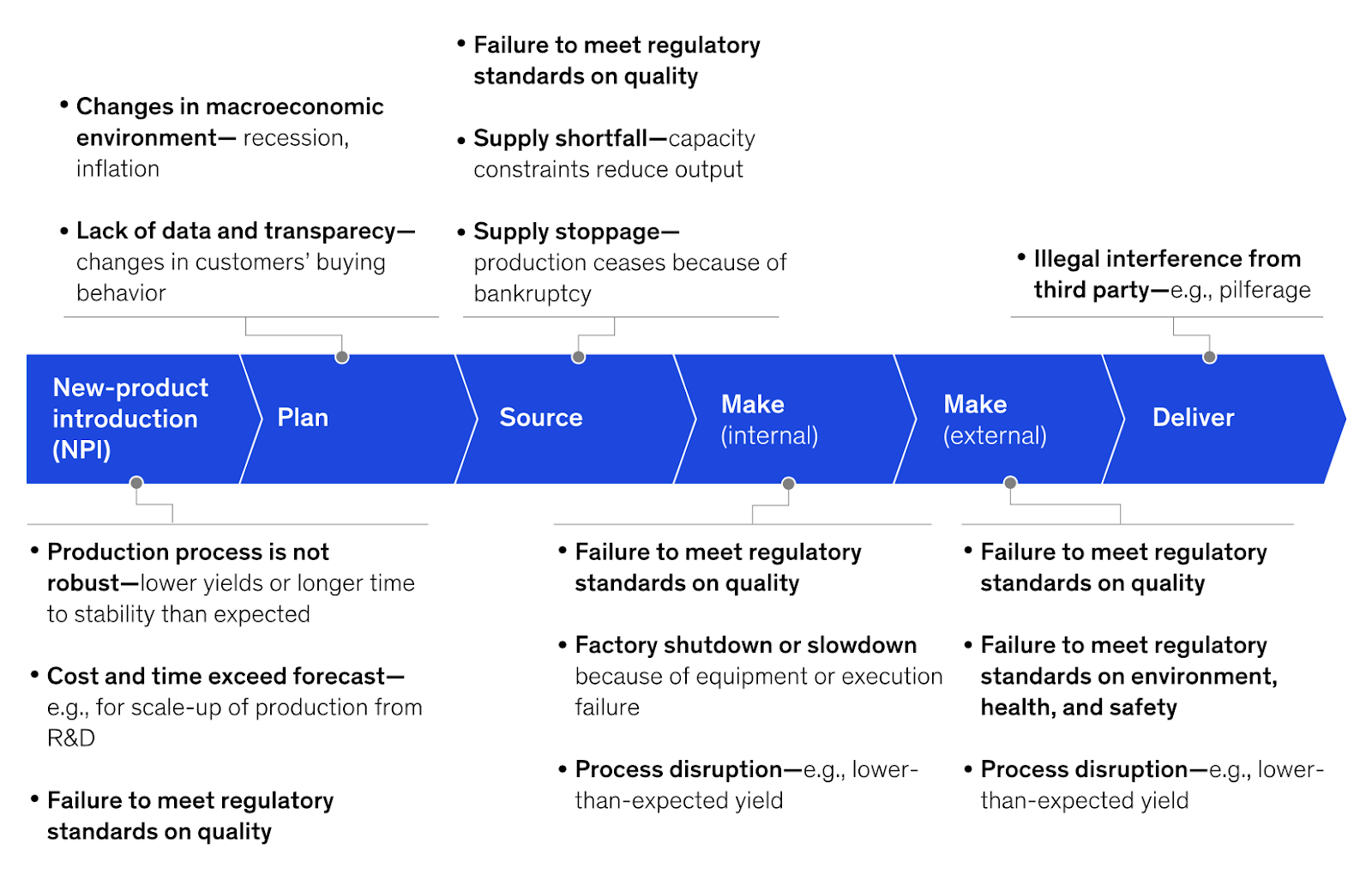
This is a very detailed example and incorporates additional risks that may or may not be relevant to you. But the more you can identify and prepare for, the better you’ll be able to respond in the future.
Once you have a risk register, you can flesh it out with mitigation strategies to minimize each risk and a set of steps to take if they become a reality.
The more detailed this information is, the better (and faster) you’ll be able to respond – limiting exposure and reducing the potential impact on your business.
You should also share this information with your supply chain partners, so that they can take similar steps to strengthen operations from end to end.
See your risks to manage your risks
Ultimately, risk management in supply chains comes down to visibility.
You can't mitigate the impact of risks without knowing what they are, and intelligent visibility tools like Beacon provide single-source-of-truth data that you can rely on to prepare for the worst.
Even if you already have a risk register in place, better visibility will allow you to sharpen it – giving a deeper insight into your risk factors, and making it easier to track changes in exposure over time.
So get in touch with us today to find out more about Beacon, and how its visibility tools can help you stay safe in a high-risk world.