INCOTERMS, short for International Commercial Terms, are a set of standardized trade terms published by the International Chamber of Commerce (ICC) that define the responsibilities and obligations of buyers and sellers in international trade transactions. They specify who is responsible for the costs, risks, and logistics involved in transporting goods from the seller to the buyer.
ISO 14083:2023 is an internationally recognized standard focusing on greenhouse gas (GHG) emissions measurement and reporting in freight transport. This standard guides organizations in assessing and managing the environmental impact of their transportation activities.
Import duties, also known as tariffs, are taxes imposed by a country's government on goods brought into the country from abroad. These duties serve several purposes: they generate revenue for the government, protect domestic industries from foreign competition by making imported goods more expensive, and sometimes regulate the volume of imports and exports.
In-gauge cargo is freight that fits within standard dimensions and weight limits, allowing for easier and more cost-effective transportation using conventional shipping methods.
Inbound logistics refers to the process of receiving, handling, and storing raw materials, components, and goods from suppliers to a business or manufacturing facility. This involves the management of various activities, such as transportation, warehousing, inventory control, and material handling.
Inbound supply chain visibility refers to the ability to track and monitor the movement of goods, materials, and shipments as they move from suppliers to a company's receiving or manufacturing facilities.
An inland transport request is a formal request to arrange the movement of goods between a port and an inland destination using land-based transportation methods like trucks or trains.
Intermodal transportation is a logistics strategy that involves using multiple modes of transport, such as trucks, trains, ships, and planes, to move goods from origin to destination. Unlike traditional transportation methods that rely on a single mode of transport, intermodal transportation combines different modes in a coordinated and seamless manner, allowing for greater flexibility, efficiency, and reliability in the supply chain.
The International Convention for Safe Containers (CSC) is a global treaty that sets safety standards for the design, inspection, and maintenance of shipping containers used in international trade.
The International Maritime Organization (IMO) is a specialized agency of the United Nations that regulates shipping and maritime safety, promoting secure and environmentally sustainable practices in the global shipping industry.
Inventory turnover refers to the efficiency with which a company manages its inventory by measuring how often inventory is sold and replaced over a specific period. It is an indicator of efficiency and liquidity in inventory management.
LCL (Less than Container Load) freight allows multiple shippers to share space in a single container, making it a cost-effective solution for smaller shipments.
Last mile delivery refers to the final leg of the logistics journey, where goods are transported from a distribution center or fulfillment center to the end destination, typically a residential address or retail store. It is considered the most critical and challenging part of the supply chain due to its complexity and impact on customer satisfaction.
When a shipper submits documentation after a defined deadline set by the carrier.
Laytime is the period of time granted to a vessel for loading and unloading cargo at a port. It represents the duration, typically in a number of days, for which the ship is allowed to remain at the port facility to complete these operations. Laytime is typically agreed upon in charter party contracts between the shipowner or operator and the charterer, who may be the cargo owner or a freight forwarder.
A Lead Logistics Provider (LLP), also known as a Lead Logistics Integrator (LLI), is a supply chain management term referring to a specialized third-party logistics (3PL) provider that takes on a central role in overseeing and coordinating an organization's entire supply chain activities.
Less than truckload (LTL) freight refers to shipments that do not fill an entire truck trailer but instead occupy only a portion of the available space. LTL shipments are typically smaller in size and weight, making them more cost-effective for businesses that do not require full truckload capacity.
In shipping, a letter of indemnity is issued by a shipper or consignee to the carrier, indemnifying them against any potential losses or liabilities arising from the release of cargo without the presentation of required documents, such as bills of lading. This document acts as a legal instrument to facilitate the smooth movement of goods in situations where original documents are unavailable or impractical to obtain.
This is the confirmation sent to the customer, shipper or consignee, that the equipment has been loaded/discharged. This message is based on the "equipment discharge/load report".
The action of lifting any cargo or container on board of the vessel for transportation.
A load board serves as an online platform or marketplace where shippers and carriers can connect to facilitate the transportation of freight. Also known as freight boards or truck load boards, these platforms provide a centralized space for posting and searching available loads and trucks, enabling efficient matching of transportation needs.
List of containers sent by the carrier or its agent to the terminal to instruct which containers must be loaded on a specific vessel/voyage. Each vessel can have several load lists in case of vessel sharing agreements.
Load optimization in logistics refers to the process of efficiently arranging and maximizing the use of available space within transportation vehicles, containers, or storage areas.
In the realm of supply chain and logistics, a load tender refers to the formal request made by a shipper or a consignee to a carrier or transportation provider to transport goods or freight from one location to another. This request initiates the process of arranging transportation services for a specific shipment.
Logistics 4.0, also known as the fourth industrial revolution in logistics, refers to the integration of advanced digital technologies and data-driven solutions to revolutionize traditional supply chain and logistics operations. It builds upon the concepts of Industry 4.0, applying automation, artificial intelligence (AI), Internet of Things (IoT), and big data analytics to optimize efficiency, visibility, and agility across the supply chain.
Logistics document management refers to the process of handling, organizing, and storing various documents involved in supply chain and logistics operations. It encompasses the management of paperwork, electronic records, and other documentation essential for the efficient flow of goods from point of origin to final destination.
Logistics route optimization involves the strategic process of determining the most efficient and cost-effective routes for transporting goods and materials from origin to destination. It aims to minimize transportation costs, reduce fuel consumption, and enhance overall delivery efficiency within supply chain and logistics operations.
A Logistics Service Provider (LSP) is a company or organization that offers specialized logistics and supply chain management services to support the transportation, storage, and distribution of goods. LSPs play a crucial role in facilitating efficient movement of products from point of origin to point of consumption, serving as intermediaries between manufacturers, suppliers, and end-users.
Logistics visibility refers to the ability of supply chain professionals to track and monitor the movement of goods and assets throughout the supply chain in real-time. It involves gaining insights into the location, status, and condition of shipments, inventory, and transportation assets as they move through various stages of the supply chain.
The manifest corrector is used to make changes to a manifest after the manifest in question has been submitted to the relevant authorities.
Marine insurance offers protection for shipments and vessels involved in maritime trade. It covers various risks, including damage to cargo caused by accidents, theft, natural disasters, and even piracy. Additionally, marine insurance can provide coverage for liabilities arising from collisions, salvage operations, and pollution incidents during transportation by sea.
A Maritime Mobile Service Identity (MMSI) number is a unique nine-digit identifier assigned to ships, coastal stations, and other maritime communication equipment. This number is used in digital selective calling (DSC), automatic identification systems (AIS), and other marine radio communication systems to ensure accurate and efficient identification and communication.
A Master Bill of Lading (MBL) is a transportation document issued by the ocean carrier or its agent to acknowledge receipt of goods for shipment. It serves as a contract of carriage between the shipper and the ocean carrier, detailing the terms and conditions of transportation, including the type, quantity, and destination of the goods being shipped. The MBL also acts as a receipt for the cargo and serves as a title document, allowing the consignee to claim ownership of the goods upon arrival at the destination port.
Material Requirements Planning (MRP) is a systematic approach to managing the manufacturing and procurement of materials necessary for production. It involves calculating the quantities of raw materials, components, and assemblies needed to fulfill production orders or meet demand forecasts within a specified timeframe.
Merchant haulage refers to a scenario in transportation logistics where the party responsible for arranging and paying for the inland transportation of goods (e.g. port to warehouse) is the cargo owner or another party distinct from the ocean carrier.
MOQ, or Minimum Order Quantity, refers to the smallest quantity of goods or products that a supplier is willing to sell or a buyer is willing to purchase in a single order. It is a contractual agreement between the supplier and the buyer, setting a threshold below which the transaction may not be economically feasible for one or both parties.
Multimodal transport refers to the transportation of goods using two or more modes of transport under a single contract. It integrates different types of transportation modes, such as road, rail, sea, and air, to optimize the efficiency of cargo movement from origin to destination.
Neopanamax ships are large cargo vessels designed to navigate the expanded Panama Canal, offering increased cargo capacity and efficiency compared to earlier Panamax vessels.
The operational capacity of a vessel on a specific voyage. This capacity takes into account all limiting factors such as the physical capacity on-board, but it also allows for constraints in the terminals to load / discharge the vessel for the specific voyage.
NVOCC stands for Non-Vessel Operating Common Carrier and refers to a type of freight consolidator or intermediary that doesn't own any vessels but functions as a carrier by issuing bills of lading, booking space on vessels, and managing shipments. Essentially, NVOCCs act as intermediaries between shippers and ocean carriers, providing shipping services without operating their own vessels.
Off dock storage refers to the practice of storing cargo containers or goods at a location separate from the port terminal or container yard where they were initially unloaded from a vessel. This storage facility, often located nearby but off-terminal, provides additional space for holding containers temporarily before they are moved to their final destination.
OTIF stands for On-Time In-Full, a key performance indicator (KPI) used in supply chain management to measure the percentage of orders delivered to customers both on time and in full. It assesses the effectiveness and efficiency of logistics operations in meeting customer expectations regarding delivery timeliness and order completeness.
Order accuracy in logistics and warehousing refers to the precision with which customer orders are fulfilled.
Order lead time, often referred to simply as lead time, is a crucial concept in supply chain management that defines the duration between the initiation of an order and its fulfillment. It encompasses the entire process from when an order is placed until the goods or services are delivered to the customer or stocked in inventory.
Out of gauge cargo, often abbreviated as OOG cargo, refers to shipments that exceed the standard dimensions or weight limitations for transportation containers or transport vehicles. This type of cargo typically includes oversized, bulky, or irregularly shaped goods that cannot fit within the standard confines of a shipping container or vehicle.
A Pre-Arrival Processing System (PAPS) number is a tracking number used in the United States for road shipments that require pre-arrival customs processing. PAPS is a border-crossing process designed to expedite the clearance of goods entering the U.S. by allowing customs to review shipment information before it reaches the border.
A Pre-Arrival Review System (PARS) number is a unique identifier used in the Canadian border clearance process for road shipments entering Canada. The PARS number allows the Canada Border Services Agency (CBSA) to review shipment information before the goods arrive at the border, facilitating faster and more efficient customs clearance.
POD (Port of Discharge) refers to the specific port where goods are unloaded from a vessel at the end of their sea voyage. This term is integral in the logistics and supply chain industry as it marks the point where cargo is transferred from the shipping carrier to the next mode of transportation, such as trucks or trains, or directly to the consignee.
POL (Port of Loading) refers to the specific port where goods are loaded onto a vessel for transportation. In international shipping, the POL is a critical point in the logistics process, marking the beginning of the goods' journey from the exporter to the importer.
A packing list is a document that itemizes the contents of a shipment. It provides detailed information about the goods being transported, including descriptions, quantities, and any special instructions for handling. This document serves as a crucial tool in supply chain and logistics operations, aiding in the verification of goods received, inventory management, and customs clearance processes.
A Panamax ship is a vessel designed to meet the size restrictions of the original Panama Canal locks.
A facility with piers or docks. Ports are accessed by vessels and represent the destinations of a voyage. Ports can contain one or more terminals.
A port call is a scheduled stop made by a vessel at a port for loading, unloading, and other operational activities related to shipping. A vessel may have several terminal calls during a single port call.
Port congestion occurs when there is a significant backlog of vessels waiting to enter or leave a port, or when there are delays in cargo loading and unloading processes within the port. It results in extended wait times for ships, increased dwell times for cargo, and overall disruptions to supply chain operations.
A port of entry refers to a designated location where goods and merchandise can legally enter a country for customs inspection and clearance. It serves as the gateway through which imported goods are received and undergo official procedures before being allowed into the domestic market.
Port pair is a term used in the shipping and logistics industry to describe a set of two ports that serve as the origin and destination in a shipping route. A port pair consists of a Port of Loading (POL) and a Port of Discharge (POD).
A Post Panamax vessel is a large ship too big for the original Panama Canal locks but smaller than newer Neopanamax vessels.
Re-export refers to the process of exporting goods that were previously imported into a country without undergoing significant alteration or manufacturing processes within that country. Essentially, re-exports involve sending imported goods back out of the country to a different destination.
Real time transportation visibility refers to the ability of supply chain professionals to monitor and track the movement of goods and shipments in real time throughout the transportation process. It involves gaining insights into the location and status of shipments as they move through various modes of transportation, such as road, rail, air, or sea.
A reefer container, also known as a refrigerated shipping container, is a specialized shipping container used to transport temperature-sensitive cargo such as fruits, vegetables, pharmaceuticals, and other perishable goods. These containers are equipped with refrigeration units to maintain specific temperature conditions throughout the journey, ensuring the freshness and quality of the cargo.
Reference number contained in the Cargo Release. It is provided by the carrier to the terminal and to the cargo receiver, and it must be presented upon pick up at the terminal.
Reverse logistics refers to the process of managing the flow of products, materials, and information from the point of consumption back to the point of origin or other designated locations. It involves activities such as product returns, repairs, refurbishment, recycling, and disposal, aimed at optimizing the value recovery and sustainability of goods throughout their lifecycle.
Roll-on/roll-off (RORO) shipping is a method of transporting vehicles and other wheeled cargo by allowing them to be driven onto and off of specialized vessels, eliminating the need for cranes or other loading equipment. RORO vessels are equipped with ramps or platforms that facilitate the easy movement of cargo.
Plan for the end-to-end shipment of a shipment. This includes specification of all transport legs, timings, schedules and interdependencies between transport legs.
SCAC stands for Standard Carrier Alpha Code. It's a unique two-to-four letter code assigned to transportation companies for easy identification in the supply chain. These codes are primarily used in the United States, Canada, and Mexico.
Safety stock, also known as buffer stock or reserve inventory, refers to the extra inventory held by a company above its average demand level. The purpose of safety stock is to provide a buffer against unexpected fluctuations in demand, supply disruptions, or lead time variability.
Sanctions screening is the process of verifying that individuals, companies, and entities involved in a business transaction are not subject to any trade or economic sanctions imposed by governments or international organizations. This process is essential to ensure compliance with legal and regulatory requirements and to avoid engaging in prohibited activities.
Scope 3 emissions refer to indirect greenhouse gas emissions generated by activities associated with an organization's value chain, including its upstream and downstream activities such as procurement, transportation, product use, and disposal. These emissions occur outside of an organization's direct control but are a result of its business activities.
A sea waybill, also known as a non-negotiable sea waybill or direct ocean carrier bill of lading, is a document issued by the carrier to acknowledge receipt of goods and confirm the contract of carriage. Unlike a traditional bill of lading, a sea waybill is not a negotiable instrument and does not require endorsement for the transfer of ownership. It serves as a receipt of shipment and a contract of carriage between the shipper and the carrier.
A single-use instrument used for securing container or freight car or truck doors.Seals have unique numbers for record purposes.
A Shipment is the realisation of a customer booking for which all containers have a common routing and details of scheduling.
Shipment visibility refers to the ability of supply chain and logistics professionals to track and monitor the movement of goods throughout the entire logistics process, from the point of origin to the final destination. It involves real-time access to information about the status and location of goods as they travel through various stages of transportation and distribution.
The shipper is the entity or party who is responsible for the shipment. This can be dependent on the INCOTERMS under which the cargo moves. If there are any queries around this, please contact your Beacon Account Manager.
A shipping alliance is a collaboration between multiple shipping companies to share resources and optimize operations, enhancing service offerings and reducing costs in the global shipping market.
An enrichment to the original booking shared by the shipper to the carrier. The shipping instruction includes volume/weight, shipping dates, origin, destination and other special instructions. The information given by the shipper through the shipping instructions is the information, which is required to create the Bill of Lading.
Shipping lanes are predetermined routes used by ships and vessels for transporting goods and commodities across oceans and seas. These routes are established to ensure safe and efficient maritime navigation, taking into account factors such as water depth, currents, weather conditions, and proximity to ports.
A shipping manifest is an essential document in the logistics process, detailing all items being transported on a ship, airplane, or vehicle. It includes information such as the names and addresses of the shipper and consignee, descriptions of the cargo, the quantity and weight of each item, and any special handling instructions. The manifest helps ensure that all parties involved in the shipping process, including customs authorities and logistics providers, have a clear understanding of the cargo being transported.
A short shipment refers to a situation in logistics where the quantity of goods received by the consignee is less than what was originally shipped or expected. It can occur due to various reasons such as inventory discrepancies, packaging errors, transportation issues, or supplier mistakes. Short shipments can disrupt supply chain operations, delay production schedules, and impact customer satisfaction.
Slotting refers to the strategic placement of products within a warehouse to optimize the efficiency of picking, packing, and shipping processes. This involves organizing products based on factors such as their size, weight, demand frequency, and compatibility with other items.
Joint term for cargo, which is not transported in a regular dry container or is considered dangerous goods. This also includes, but is not limited to out of gauge cargo.
All container types other than regular Dry or Reefer containers. Examples of these can be flat racks (open containers for oversized, irregular and/or heavy cargo), Open tops (fitted with a solid removable roof), etc.
A stockout occurs when a business runs out of a particular item or product, leading to its temporary unavailability for sale or distribution. It denotes a situation where customer demand exceeds available inventory, resulting in potential lost sales and customer dissatisfaction.
Stowage refers to the systematic loading and arrangement of cargo on a vessel to ensure safety, efficiency, and optimal use of space during transportation.
Supplier risk management is the process of identifying, assessing, and mitigating risks associated with a company's suppliers to ensure continuity and reliability in the supply chain.
Supply Chain 3.0 represents the evolution of traditional supply chain management practices into a more advanced and interconnected model, driven by digital technology and data analytics. This next-generation supply chain approach focuses on enhancing visibility, agility, and collaboration across the entire supply chain ecosystem.
Supply Chain 4.0, an integral part of the broader concept of Industry 4.0 and Logistics 4.0, represents a paradigm shift in supply chain management driven by digital technologies and advanced analytics. It encompasses the integration of artificial intelligence (AI), machine learning, robotics, and the Internet of Things (IoT) to create smarter, more connected, and automated supply chain networks.
Supply chain automation involves the use of technology and software systems to streamline and optimize various processes within the supply chain, including inventory management, order fulfillment, transportation, and warehouse operations. It aims to reduce manual intervention, improve efficiency, and enhance overall supply chain performance.
Supply chain collaboration refers to the strategic partnership and cooperation among different entities within the supply chain, including suppliers, manufacturers, distributors, warehouses and retailers. It involves sharing information, resources, and responsibilities to optimize processes, improve efficiency, and achieve common goals.
A supply chain control tower is a centralized hub or platform that provides end-to-end visibility and orchestration of supply chain operations in real-time. It acts as a command center where supply chain professionals can monitor, analyze, and manage the flow of goods, information, and finances across the entire supply chain network.
Supply chain data refers to the information generated and collected throughout the entire supply chain process, from procurement of raw materials to delivery of finished products to customers. It encompasses various types of data, including inventory levels, transportation routes, freight tracking milestones, supplier performance, demand forecasts, and customer preferences. Supply chain professionals can analyze this data to gain insights, optimize processes, and make informed decisions to improve efficiency and planning.
Supply chain finance (SCF) refers to a set of financial solutions and practices aimed at optimizing cash flow and working capital management throughout the supply chain. It involves leveraging financial instruments and services to facilitate transactions between buyers, suppliers, and financial institutions, thereby improving liquidity, reducing risk, and enhancing collaboration within the supply chain.
Network design in supply chain management involves creating a strategic framework that outlines the structure and operations of the supply chain.
Supply chain resilience refers to the ability of a supply chain to withstand and recover from disruptions while maintaining continuous operations and delivering products or services to customers without significant impact. It involves the capacity to anticipate, adapt, and respond effectively to various challenges, including natural disasters, geopolitical events, market fluctuations, and supplier disruptions.
Supply chain risk management refers to the process of identifying, assessing, and mitigating risks within a supply chain to ensure continuity and minimize disruptions. It involves analyzing all elements of the supply chain—from sourcing raw materials to delivering finished products—to anticipate and address potential vulnerabilities that could impact operations, finances, or reputation.
Supply chain traceability refers to the ability to track and verify the journey of products through every stage of the supply chain, from raw materials to the final consumer.
Also referred to as end-to-end visibility, supply chain visibility refers to the ability of organizations to track, analyze, communicate and monitor the flow of goods as they move across the entire supply chain, from raw material suppliers to end customers. It encompasses real-time data and insights into inventory levels, order statuses, transportation movements, and other key metrics, enabling stakeholders to make informed decisions and respond swiftly to changes and disruptions.
Supply planning is the process of aligning supply with demand to ensure that sufficient quantities of goods or materials are available to meet customer needs while minimizing costs and optimizing inventory levels. It involves forecasting demand, determining production or procurement requirements, scheduling production activities, and managing inventory levels to maintain a balance between supply and demand.
A facility for loading, moving or discharging containers. Terminals can be both inland terminals for trucks and rail or port terminals are accessed by vessels and these can contain multiple berths.
Upon completion of operations on a particular vessel, a terminal departure report (TDR) is to be sent to the respective shipping lines. This report, prepared from timesheets, includes container vessel operation data and tabulation of productivity. This can be in the form of the EDI-message TPFREP.
Each terminal has a set number of moves, which can be performed on a vessel during a port call. One move is usually defined as the movement (loading or unloading) of one container.
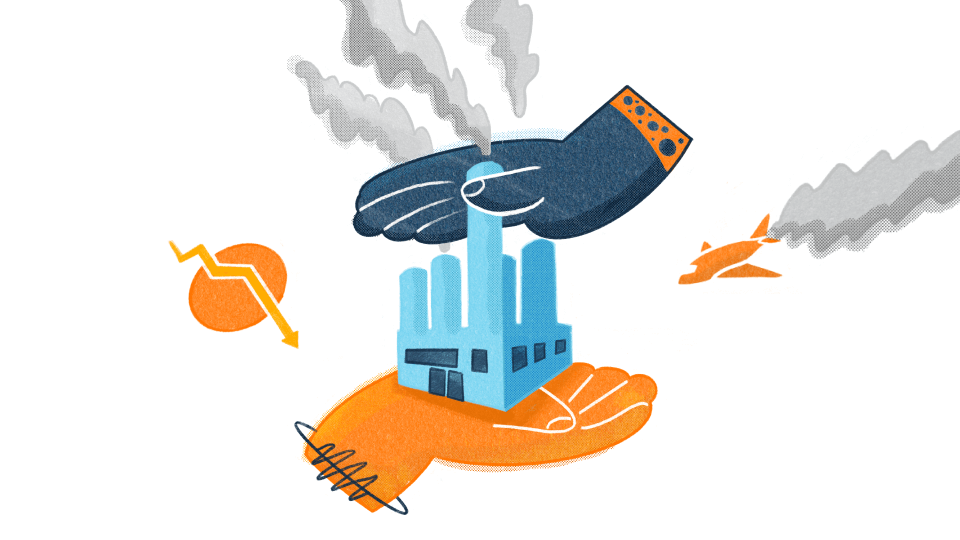
Supply chain decarbonization: A step-by-step voyage to sustainable efficiency
There’s always room for supply chains to be better. But that doesn’t just mean making them faster, more reliable, or easier to track.
That’s all great, of course, and really important for movers of goods, but the elephant in the room is the impact on our planet.
Global supply chains are responsible for a huge proportion of the world’s carbon, and make up around 90% of the average business’s greenhouse gas emissions.
That’s something that has to change for a sustainable future, and the good news is that companies are starting to stand up and take action.
In fact, supply chain decarbonization is quickly becoming a business priority, with 94% of organizations that signed up to the Science Based Targets Initiative (SBTi) in 2020 making commitments to reduce emissions directly and through their relationships with customers and suppliers.
We know that reducing supply chain emissions isn’t always as easy as it should be, so let’s take a closer look at a few steps every business can take to start moving the needle.
Step 1: Assess your own carbon emissions
Decarbonization starts at home and every business has the power to make a difference – big or small.
So before you get into the details of what your partners are doing, make sure you’ve got a clear understanding of your emissions and how you might be able to reduce them.
Measuring your emissions, wherever they are
As a first step, you’ll need to work out what your direct emissions are. These are typically split into two categories – Scope 1 and Scope 2:
- Scope 1 emissions are all the emissions that a business has first-hand responsibility for, including everything from fuels burnt during production and the running of company-owned vehicles through to the impact of an air conditioning system.
- Scope 2 emissions are a little further out of your control, and are made up of the emissions that come when you purchase any energy from a third party.
For most businesses, these two categories are relatively easy to measure if you’re collecting the right data around energy used on-site and energy purchased.
But if you’re not sure where to start, the American Environmental Protection Agency has published some helpful guidance on Scope 1 and Scope 2 Inventory Guidance that covers different methods for collecting and reporting accurate information.
Setting targets
With up-to-date Scope 1 and Scope 2 emissions data, the important work of reducing emissions can begin.
But to make sure you’re moving in the right direction, it’s always best to have a clear idea of the targets you want to reach and how you’ll reach them.
Those Science Based Targets that we mentioned earlier are specially developed goals designed to limit global temperature increases to less than 1.5°C.
They apply to every area of the supply chain, and are customizable to suit the needs and current sustainability standards of your business.
That flexibility is essential, because where one business might set a science based target of reaching net zero within 10 years, another may be able to get there sooner – or take a little longer.
It’s a great process, because once you’ve submitted a target, the SBTi will review your submission, check it against a science-based criteria, and then give you detailed feedback on whether it’s appropriate and realistic.
For example, one of Maesrk’s Science Based Targets is to reduce absolute scope 1 and 2 GHG (greenhouse gas) emissions 42% by 2030 from a 2021 base year. They have also committed to reduce absolute scope 3 GHG emissions from upstream transportation and distribution 42% within the same timeframe.
Reducing your direct carbon emissions
Whether your business decides to formally commit to a target in line with the SBTi’s criteria or not – once you’ve set goals, there are plenty of ways to reach them.
At a Scope 1 level, streamlining processes, investing in EVs, and anything else that cuts your carbon consumption will add up quickly.
While for Scope 2, the biggest immediate change you can make is switching to a low-carbon energy supplier, or even producing your own renewable energy.
For both scopes, you can also use Beacon’s partnership with Lune to offset any carbon use you can’t eliminate, for a truly net-zero impact.
Step 2: Go a step further with supply chain emissions
As well as Scope 1 and 2, there’s a third type of emissions called (you guessed it) Scope 3 emissions.
This is where your supply chain comes into play, with scope 3 being a much broader category that includes all of the indirect carbon emissions connected to your business.
This is where a lot of supply chain emissions sit, with every part of the process having an impact.
That’s one of the reasons why it’s so important to invest in supply chain visibility – because without it there’s almost no way of knowing how much carbon is being generated as a byproduct of your day-to-day operations.
Understanding and measuring supply chain emissions
In the past, untangling Scope 3 supply chain emissions from your full network of partners would be a complex, if not impossible, job due to the use of inconsistent methodologies.
But Beacon’s supply chain sustainability software cleans things up.
Our carbon tools show emissions across the supply chain, drawing on key data like distance traveled, shipment weight and vessel characteristics.
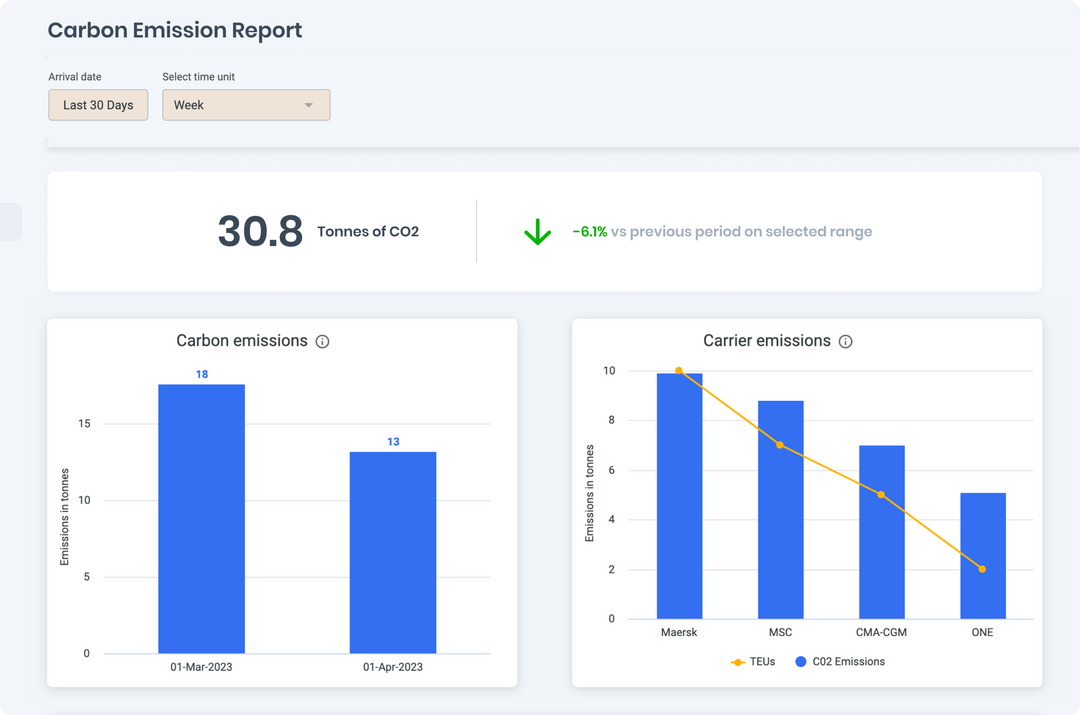
Reducing supply chain emissions and setting supplier standards
With Beacon’s insights, there are a few different ways to reduce your carbon footprint. You might want to use our data to select routes or carriers with a reduced impact. Or directly offset your scope 3 emissions in just a few clicks from your Beacon dashboard.
Beacon’s tech can help with all that. But there’s another way to go even further.
Share! Share your insights with partners and direct them towards helpful resources like the Carbon Disclosure Project (CDP) to help them better benchmark their performance.
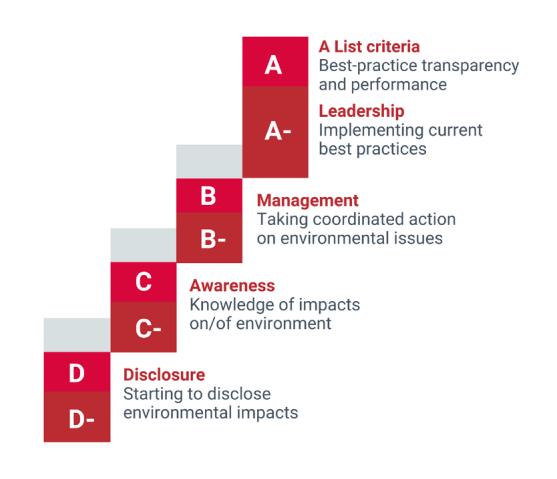
You can also use CDP scores to decide what types of businesses you want to work with.
That might mean incentivizing supply chain decarbonization with discounts or bulk deals for more responsible partners.
Or even going a step further and committing to only working with suppliers that meet a certain sustainability score – and ensuring that they’re committed to it during the onboarding process.
With Beacon, it’s all easy to track, giving you more control over scope 3 supply chain emissions and the global impact of your business.
Step 3: Make transparency central to sustainability
Whatever steps you take to reduce supply chain emissions and decarbonize your business, it’s always good to be open and honest with customers about what you’re doing and why.
We live in a world where responsibility really matters. So sharing the moves you’re making – with real data to back it all up – is one of the best ways to reassure everyone who engages with your business that you’re a partner with the right ethics.
That applies just as much to your partners, even if they aren’t quite as advanced on their sustainability journeys.
Regular updates and information shared between partners can foster a powerful sense of community across supply chains, with everyone helping each other reach their goals and contribute to making a difference together.
That’s the power to change in action. And better supply chain visibility is its foundation.
So take the next big step on your decarbonization journey today with supply chain sustainability software that goes the extra mile.