ABC Analysis is a method used in supply chain management to categorize inventory into three groups—A, B, and C—based on their importance. This classification helps businesses prioritize their resources and focus on the most critical items.
An Advanced Shipping Notice (ASN), sometimes referred to as Advance Ship Notice, is a notification sent by a supplier or manufacturer to a customer or retailer to provide detailed information about a pending shipment. The ASN serves as an electronic document that outlines the contents of the shipment before it physically arrives at the destination.
An agile supply chain is a flexible and responsive approach to supply chain management that enables organizations to quickly adapt to changing market conditions, customer demands, and disruptions. It focuses on enhancing speed, efficiency, and adaptability throughout the entire supply chain process, from sourcing raw materials to delivering finished products to customers.
An air waybill (AWB) is a vital logistics document used in air freight transportation. It serves as a contract of carriage between the shipper (consignor) and the airline (carrier), detailing the terms and conditions of air transportation for the shipment. The air waybill contains essential information such as the origin and destination of the cargo, the description of goods, the weight, and the freight charges.
An arrival notice is a notification sent by a carrier or freight forwarder to inform consignees or recipients that a shipment has arrived at its destination port or facility. This notice serves as an important communication tool in the supply chain, providing recipients with essential information about the arrival of their goods and detailing the next steps for delivery or pickup.
An Automatic Identification System (AIS) is a tracking system used in the maritime industry to monitor the location and movement of ships. AIS provides real-time information about vessel identification, position, course, and speed.
Backhauling is a transportation logistics practice where trucks carry a return load on their way back from delivering goods to their destination. Instead of returning empty, trucks utilize their empty space to transport goods from the destination back to the point of origin or another destination along the route.
In supply chain management, "backorder" refers to a situation where a customer places an order for a product that is temporarily unavailable in the seller's inventory. When an item is on backorder, it means the customer's order cannot be fulfilled immediately due to insufficient stock levels.
A bay plan is a diagram that details the stowage of containers on a vessel, specifying their exact position by bay, row, and tier to ensure efficient and safe loading and unloading operations.
A Beneficial Cargo Owner (BCO) is the entity with ownership or a beneficial interest in transported goods. While not always the shipper, the BCO reaps the benefits of the cargo's arrival.
A bill of lading (B/L) is a legal document issued by a carrier or its agent to acknowledge receipt of goods for shipment. It serves as a contract between the shipper (seller) and the carrier (transport provider), detailing the terms and conditions of transportation, including the type, quantity, and destination of the goods.
Blank sailing is a term used to describe the situation when a shipping line cancels a scheduled port call or an entire voyage. This can happen for various reasons, such as low demand for shipping services, operational issues, or unforeseen circumstances like bad weather or port congestion.
A blind shipment refers to a logistics practice where certain details about the shipment, such as the sender, receiver, or contents, are intentionally obscured or withheld from one or both parties involved in the transaction. This is typically done to maintain confidentiality or to prevent competitors from obtaining sensitive information about suppliers, customers, or pricing.
A bonded warehouse is a secured facility authorized by customs authorities where imported goods can be stored, manipulated, or undergo manufacturing operations without payment of duty.
A booking confirmation is a document that verifies the reservation of space for cargo on a carrier’s vessel, flight, or truck, ensuring all shipping arrangements are approved and scheduled.
A request for reservation of space and equipment for a particular vessel/voyage and possibly inland transport.
Break bulk cargo refers to goods that are individually packaged or bundled, rather than being transported in containers or in bulk. These items are often large or irregular in size and include products like machinery, vehicles, construction materials, or heavy equipment.
Buffer stock, also known as inventory buffer or stock buffer, refers to the extra inventory held by a company to mitigate the risk of stockouts caused by uncertainties in supply and demand. It acts as a cushion against fluctuations in customer demand, supply chain disruptions, and variations in lead times.
Bulk cargo refers to commodities that are transported unpackaged in large quantities, typically stored and handled in bulk form, rather than in individual units or containers. This category of cargo is crucial in global trade, especially for goods that are homogeneous and not easily damaged during transportation.
The bullwhip effect, also known as demand amplification or whiplash effect, is a phenomenon that occurs in supply chains where small fluctuations in demand at the consumer level lead to exaggerated fluctuations in demand further upstream in the supply chain. This amplification of demand variability causes inefficiencies, such as excess inventory, stockouts, and increased costs, as supply chain partners overreact to perceived demand changes.
CIF, or Cost, Insurance, and Freight, is an international shipping agreement used in the transportation of goods. In freight shipping, CIF means that the seller takes responsibility for the cost of transporting goods to the buyer's destination port. This includes paying for shipping, handling, and insurance. The seller's obligations end when the goods reach the destination port, at which point the buyer assumes responsibility for customs clearance, import duties, and any further transport to their final destination.
A Capesize ship is a large bulk carrier vessel designed to transport heavy raw materials across long distances, too large to transit through canals like the Panama or Suez.
The action of allowing cargo to leave the container yard typically authorized by the carrier. This is often confused with gate-out, but cargo release is the authorization necessary before shipments can be allowed to gate-out.
A cargo survey is an inspection process that assesses the condition and quantity of goods during transportation to ensure compliance with shipping terms and prevent disputes.
A shipping carrier is an organization that provides transportation services for goods. They manage the logistics of moving cargo, which includes loading, transporting, and delivering goods to the specified location. Shipping carriers handle various types of shipments, from small packages to large freight consignments, using different modes of transportation such as maritime, air, rail, and road.
Carrier haulage refers to a transportation arrangement where the carrier, typically the ocean shipping line or its designated transport provider, is responsible for arranging and paying for the inland transportation of containers. In this scenario, the carrier takes charge of moving the container from the port of discharge to the final destination or vice versa, using their own transportation assets or subcontracted carriers.
A carrier scorecard is a performance measurement tool used by supply chain and logistics professionals to evaluate the effectiveness and reliability of their freight carriers. It provides a standardized way to assess carriers based on various performance metrics, helping organizations make informed decisions about their logistics partners
A certificate of origin is a document issued by an authorized body or organization that certifies the country in which the goods being shipped were manufactured, produced, or processed. It serves as a declaration by the exporter to the customs authorities of the importing country, providing information about the origin of the goods and facilitating trade by ensuring compliance with trade agreements, tariffs, and regulations.
A commercial invoice is a crucial document used in international trade transactions to provide details of the goods being shipped and their corresponding value. It serves as a formal request for payment from the buyer to the seller and is essential for customs clearance and regulatory compliance.
In shipping, a commodity refers to bulk goods or raw materials that are transported in large volumes as part of global trade.
In the realm of supply chain and logistics, the term "Consignee" refers to the individual, company, or entity to whom a shipment of goods is delivered. The consignee is the designated recipient or receiver of the goods, typically identified by name and address on shipping documents such as the bill of lading or delivery order.
Consignment inventory is a supply chain arrangement where a supplier (consignor) retains ownership of goods while they are held at a customer's (consignee's) location. The consignee only pays for the goods when they are sold or consumed, and the supplier retains responsibility for managing and replenishing the inventory as needed.
In shipping and logistics, a consignor refers to the entity or person who is the sender or shipper of goods. The consignor is responsible for initiating the shipment of goods from one location to another, typically to a consignee or recipient.
A container depot is a facility used for the storage, maintenance, and repair of empty shipping containers when they are not actively in use for transportation.
Container discharge is the process of unloading shipping containers from a vessel at a port, using cranes and other equipment, for onward transportation.
A container freight station (CFS) is a designated facility where goods are received, sorted, and prepared for onward transportation, enhancing efficiency in logistics operations.
Shipping container grades classify containers based on their condition and suitability for transporting goods, ranging from cargo-worthy to as-is quality.
A container packing certificate is a document that verifies the proper packing and loading of goods into a shipping container. It attests that the contents have been securely packed, arranged, and secured according to industry standards and regulatory requirements. Obtaining a container packing certificate is crucial for compliance with international shipping regulations and contractual obligations. It provides assurance that the goods have been properly prepared for transport, minimizing the risk of delays, damages, or disputes during the shipment process.
A container rollover occurs when a shipping container is not loaded onto its scheduled vessel and is instead 'rolled over' to a subsequent vessel. This delay means the container misses its intended departure and must wait for the next available sailing, which can significantly impact lead times and delivery schedules.
Container stripping (devanning) is the process of unloading cargo from a shipping container at its destination for inspection, storage, or further distribution.
Container stuffing is the process of loading cargo into a shipping container in a safe and space-efficient manner for transportation.
Cross docking is a logistics strategy where incoming goods from suppliers are unloaded from incoming trucks or containers and directly loaded onto outbound trucks or trailers, with minimal or no storage time in between. Essentially, it involves transferring goods directly from the inbound dock to the outbound dock, bypassing the need for traditional warehousing storage.
A customs broker is a licensed professional who specializes in facilitating the clearance of goods through customs barriers for importers and exporters. Acting as intermediaries between businesses and customs authorities, customs brokers ensure compliance with regulations and smooth passage of goods across international borders.
Customs clearance refers to the process of fulfilling the legal requirements necessary to facilitate the import or export of goods across international borders. This procedure ensures that shipments comply with local laws and regulations, allowing them to enter or leave a country legally. It involves various documentation, inspections, and payments of duties and taxes.
A customs manifest lists in detail all the bills of lading issued by a carrier, its agent or master for a specific voyage and port call. It is a detailed summary of the total cargo of a vessel and is used principally for customs purposes. It acts as a declaration to customs authorities, ensuring compliance with regulations and facilitating smooth movement of goods through ports and checkpoints.
The latest point in time where a container has to be delivered to a terminal to be loaded on a vessel, or where certain documentation has to be provided by the Shipper.Example: CY cut-off, FCL cut-off, VGM cut-off, DG cut-off.
Cycle counting is a methodical approach to inventory management where a subset of inventory is counted on a continuous basis, typically throughout the year. Unlike traditional annual or periodic inventory counts that halt operations, cycle counting allows businesses to maintain regular operations while ensuring accurate stock levels.
DAP, or Delivered At Place, is a term used in international trade that specifies the seller's obligation to deliver goods to a designated location in the buyer's country. In DAP terms, the seller is responsible for all costs and risks associated with delivering the goods to the agreed-upon destination. This includes arranging transportation, handling charges, and insurance up to the point of delivery. The buyer, however, is responsible for unloading the goods, handling customs clearance, and paying any import duties and taxes once the goods arrive at the destination.
DDP (Delivered Duty Paid) shipping terms dictate that the seller assumes all responsibilities and costs associated with delivering the goods to the buyer's specified destination. This includes transportation, insurance, handling charges, and import duties and taxes. Essentially, the seller handles everything from the point of origin to the final delivery location, ensuring the goods arrive ready for use by the buyer without any additional costs or logistical burdens.
DDU, or Delivered Duty Unpaid, is an international shipping term that defines the responsibilities of the seller and buyer. Under DDU terms, the seller delivers the goods to a specified destination in the buyer's country, covering all costs and risks associated with transportation, except for duties, taxes, and other import charges which are the responsibility of the buyer. The seller's obligations include arranging and paying for freight, insurance, and handling charges until the goods reach the agreed-upon place.
DPU, or Delivered at Place Unloaded, is a term used in international trade that specifies the seller's responsibility to deliver and unload goods at a designated location in the buyer's country. Under DPU terms, the seller bears all costs and risks associated with transporting and unloading the goods at the agreed destination. This includes all transportation costs, including freight, insurance, and handling charges, up to and including the unloading of the goods at the destination. The buyer then takes over responsibility for import duties, taxes, customs clearance, and any further transport to the final destination.
A dangerous goods declaration (DGD) is a legal document required for the transportation of hazardous materials or dangerous goods by air, sea, road, or rail. It provides detailed information about the nature, classification, packaging, and handling requirements of the dangerous goods being transported. The DGD helps ensure compliance with international regulations and facilitates the safe handling and transport of hazardous materials throughout the supply chain.
Deadheading is the practice of operating a commercial vehicle, such as a truck or a trailer, without any cargo or paying passengers. Essentially, it refers to the movement of a vehicle while it is empty, either on its way to pick up a load or after delivering a load to its destination.
Deadweight tonnage (DWT) is a measure of a ship's carrying capacity, representing the total weight of cargo, fuel, crew, provisions, and other materials that the vessel can safely carry.
Demurrage refers to the additional charges imposed on the owner or operator of a vessel, freight car, or truck for delaying the use of equipment or facilities beyond the agreed-upon time. In the context of maritime shipping, demurrage applies to the time that cargo remains at the port or terminal beyond the allotted free time for loading or unloading.
Detention charges are fees incurred when a carrier's equipment, such as containers or trailers, is held beyond the agreed-upon free time at a facility, such as a port, terminal, or warehouse. These charges compensate the carrier for the additional time their equipment is detained and unavailable for other use.
A supply chain digital twin replicates the entire supply chain network, including assets, facilities, products, and processes, in a digital environment. It enables real-time monitoring, analysis, and simulation of supply chain operations to improve efficiency, optimize decision-making, and mitigate risks.
Dimensional weight, also known as volumetric weight, is a pricing technique used by shipping carriers to calculate the cost of shipping packages based on their volume rather than just their actual weight. This method helps carriers account for the space that a package occupies in relation to its weight, ensuring fair pricing for shipping services.
A dock receipt is a logistics document issued by a carrier or its agent to acknowledge the receipt of goods at a shipping dock or terminal for transportation. It serves as a temporary receipt until the goods are loaded onto a vessel or other mode of transportation for shipment to their destination. The dock receipt contains essential information about the cargo, such as the quantity, description, condition, and destination, along with details about the carrier, shipper, and consignee.
A ship’s draft (draught) measures the depth of the vessel below the waterline, which determines the minimum water depth required for safe navigation.
Drayage refers to the transportation of goods over a short distance, typically within the same metropolitan area or between nearby facilities. It plays a crucial role in the logistics and supply chain industry, linking various points in the transportation network, such as ports, rail terminals, and distribution centers. Drayage often involves moving goods from a transportation hub like a port to a nearby warehouse or vice versa.
Drop shipping is a retail fulfillment method where a store doesn’t keep the products it sells in stock. Instead, when a store sells a product using the drop shipping model, it purchases the item from a third party and has it shipped directly to the customer.
Dry bulk cargo refers to unpackaged, loose commodities that are shipped in large quantities and typically consist of raw materials. These goods are usually loaded directly into the holds of a vessel without any packaging, making them different from containerized or break bulk cargo.
A booking received via Electronic Data Interchange, a standard electronic format for exchanging business documents within the supply chain, such as purchase orders, invoices, shipping notices, and other transactional information.
An Economic Operators Registration and Identification (EORI) number is a unique identifier assigned to businesses engaged in international trade within the European Union (EU) and certain other countries. It serves as a means of tracking and identifying entities involved in import, export, and other customs-related activities.
In shipping, ETA refers to the anticipated arrival time of a vessel, truck, or aircraft at a specified port or delivery location. It is calculated based on various factors such as the departure time, transit duration, and any potential delays due to weather, customs, or other unforeseen circumstances. This prediction helps logistics professionals plan and coordinate the movement of goods, ensuring timely deliveries and efficient supply chain management.
EXW, or Ex Works, is one of the Incoterms (International Commercial Terms) published by the International Chamber of Commerce (ICC). It defines the responsibilities of buyers and sellers in international transactions. Under EXW terms, the seller fulfills their obligation by making the goods available for pickup at their premises (factory, warehouse, etc.). The buyer assumes all risks and costs associated with transporting the goods from the seller’s location to the final destination.
Economic Order Quantity (EOQ) is a fundamental concept in inventory management that determines the optimal quantity of goods a company should order to minimize total inventory costs. It balances the costs of holding inventory (holding costs) and the costs of ordering inventory (ordering costs) to find the most cost-effective quantity to order at any given time.
An Electronic Product Code (EPC) is a unique identifier used to distinguish individual items, cases, or pallets in the supply chain. It serves as a digital identifier that provides a standardized way to track and manage products throughout their lifecycle, from manufacturing to distribution to retail.
Used for storing cargo in/on during transport. The equipment "size/type" is defined by the ISO 6346 code. The most common equipment size/type is 20'/40'/45' Dry Freight Container, but a number of different versions exist.
Confirmation & receipt of the equipment loaded/discharged on a vessel during a port call. This information is recorded by the terminal operator and sent to the carrier. This is often done using the EDI message - COARRI. The COARRI message reports that the equipment specified have been discharged from a seagoing vessel (discharged as ordered, over landed or short landed), or have been loaded into a seagoing vessel.
A shipping exception is an unexpected event or disruption that causes a shipment to deviate from its planned delivery schedule.
Expedited freight refers to a specialized service in logistics and supply chain management aimed at transporting goods quickly and efficiently to meet tight delivery deadlines. It is used when standard shipping methods cannot meet the required delivery timeframe, typically due to urgent customer needs, production delays, or unforeseen circumstances.
FAS, or Free Alongside Ship, is a shipping term used in international trade that specifies the seller's responsibilities and costs up to the point where goods are placed alongside the buyer's vessel at the designated port of shipment. The buyer then assumes all risks and costs from that point forward.
FCA, or Free Carrier, is an Incoterm (International Commercial Term) used in international trade to define the point at which the seller's obligations are fulfilled and the buyer assumes responsibility for the goods. Under FCA, the seller delivers the goods, cleared for export, to the carrier or another party nominated by the buyer at a specified place.
FCL (Full Container Load) freight involves shipping an entire container for a single shipper, offering faster and more secure transport, especially for large-volume cargo.
FOB, or Free on Board, is a term used in international trade to indicate when ownership and liability for goods transfer from the seller to the buyer. It specifies the point at which the seller is no longer responsible for the goods. This term is crucial for determining who pays for shipping, insurance, and other logistics costs, as well as who bears the risk during transit.
An entity operating a feeder service - ref. Feeder vessel.
A container feeder vessel, also known as a feeder ship, is a relatively small cargo vessel that is specifically designed for transporting containers between smaller ports or terminals to larger hub ports where mainline vessels operate. These vessels serve as a crucial link in the global shipping network by facilitating the distribution of cargo to and from regional ports that may not be accessible to larger ships due to navigational constraints or limited infrastructure.
A Feedermax container ship is a medium-sized vessel used to transport containers between regional ports and major ports, connecting smaller markets to global shipping routes.
Fill rate in supply chain management refers to the measurement of how fully customer demand for a product or service is met through the availability of inventory. It indicates the percentage of customer orders or demand that can be fulfilled immediately from stock, without backorders or delays.
A "Flag of Convenience" (FOC) refers to the practice of a ship's owner registering a merchant vessel in a country other than the owner’s country of origin to benefit from more favorable regulations, often related to taxes, labor laws, and safety standards. This practice allows shipowners to operate under less stringent regulations, often reducing operational costs and increasing profitability. However, FOC can also lead to concerns about safety, environmental standards, and working conditions for crew members, as the regulatory oversight in these flag states might not be as rigorous.
4PL, or Fourth Party Logistics, refers to a logistics model where a single organization, known as the fourth-party logistics provider, takes on the responsibility of managing and coordinating the entire supply chain on behalf of the client. Unlike traditional third-party logistics (3PL) providers, who primarily handle specific logistics functions, 4PL providers offer comprehensive end-to-end supply chain management services. 4PL providers act as strategic partners, overseeing multiple 3PLs and other service providers to optimize supply chain operations, enhance efficiency, and achieve cost savings for their clients.
A free trade zone (FTZ) is a designated area within a country where goods can be imported, stored, manufactured, or exported without being subject to the usual customs duties and tariffs.
A freight forwarder is a vital link in the supply chain, specializing in the coordination and management of international shipments. Acting as an intermediary between shippers and carriers, freight forwarders handle various logistics tasks such as booking cargo space, arranging transportation, preparing documentation, and managing customs clearance.
Freight visibility (also called shipment visibility) refers to the ability of supply chain professionals to track and monitor the movement of freight shipments throughout the supply chain. It involves gaining real-time insights into the location and status of goods as they move through various transportation modes and stages of the logistics process.
Full truckload (FTL) freight refers to shipments that occupy the entire capacity of a truck trailer. Unlike less than truckload (LTL) shipments, FTL shipments do not share space with other cargo, allowing for direct transportation from the point of origin to the destination without intermediate stops.
The GLEC (Global Logistics Emissions Council) framework is a globally recognized standard developed to measure and report greenhouse gas (GHG) emissions from logistics activities. It provides guidelines and best practices for calculating emissions across various modes of transport, including road, rail, sea, and air.
The action of moving a container from a container yard, a terminal or another restricted/controlled area.
The German Supply Chain Act, also known as Lieferkettengesetz, is a landmark legislation enacted to promote corporate social responsibility and ensure ethical practices throughout global supply chains. Introduced in 2021, the law applies to German companies with over 3,000 employees, requiring them to monitor and address human rights abuses, environmental violations, and labor standards in their supply chains.
A Global Trade Item Number (GTIN) is a unique identifier assigned to products in the supply chain to facilitate efficient tracking and management from production to point of sale. It provides a standardized method for identifying items globally, ensuring accurate inventory control, and enabling seamless transactions between trading partners.
A Goods Receipt Note (GRN) is a document used in the process of confirming the receipt of goods from a supplier or vendor. It serves as an acknowledgment by the receiving party, typically a warehouse or a buyer, that the goods specified in the accompanying purchase order have been received in satisfactory condition.
Green logistics refers to the process of minimizing the environmental impact of logistics and supply chain activities, including transportation, warehousing, packaging, and distribution.
A Handysize ship is a small to medium-sized bulk carrier designed for transporting various cargo types, capable of navigating smaller ports and shallow waters.
Gear used to do inland transportation of a container. This can include tools and apparatus used to load/discharge the container onto the intermodal type.
Specifications for a haulier set by a carrier in regards to a specific work order, e.g. timeline, capabilities.
The joint term for merchant and carrier haulage. It should be noted that a shipment can have several types of haulage throughout the transport from origin to destination.
A haulier, also known as a trucking company or a carrier, is a business or individual that transports goods by road using trucks or lorries. Hauliers play a vital role in the transportation industry, moving goods between locations such as warehouses, distribution centers, manufacturing facilities, ports, and retail stores.
A House Bill of Lading (HBL) is a transportation document issued by a freight forwarder or Non-Vessel Operating Common Carrier (NVOCC) to acknowledge receipt of goods for shipment. It serves as a contract of carriage between the shipper and the carrier and includes details such as the type, quantity, and destination of the goods being transported.
In supply chain logistics, a hub and spoke model refers to a system where goods or services are transported through a central hub to various spoke locations. The hub acts as a central point for collection, sorting, and distribution, while the spokes represent the routes connecting the hub to different destinations.
.png)
How to Mitigate Risks in Holiday Container Shipping
Along with cheer, the holiday season brings with it an inevitable surge in cargo shipping volumes to accommodate increased consumer spending. This rush puts immense pressure on global logistics operations. For shippers, this period presents a host of risks and challenges ranging from vessel capacity constraints to port congestion, overcrowded warehouses, last-mile delivery challenges and increased reverse logistics activity.
As we enter the busiest shopping months of the year, it is critical for wholesale distributors and retailers to prepare, adapt and optimize their shipping strategies in order to protect their supply chains, meet the demands of consumers and ensure high service levels throughout the period.
Stresses in holiday shipping
The holiday rush is most often associated with Black Friday, Christmas and Boxing Day shopping in November and December. However, other holiday seasons around the globe also see spikes in consumer buying and associated supply chain pressures. According to Maersk, other peak logistics periods include:
- Lunar New Year: January or February in much of Asia, following which it takes four to six weeks for factories and port operations to return to normal levels after the holidays.
- Carnival: February or March in Brazil.
- Summer Holidays: July-August in the northern hemisphere and December-January in the southern hemisphere
During holiday periods, consumers expect faster shipping and hassle-free returns. This puts pressure on shippers and retailers to meet those expectations while maintaining quality and timeliness.
These peak volumes create stress in supply chains especially around warehousing, distribution, fulfillment, last mile and reverse logistics. Shippers should recognize these pressure points and make a plan for handling the increased demand.
Staying on top of shipments in the build up to Q4 can be overwhelming. Real-time visibility tools can streamline your workflows and save you precious time. A good visibility tool will facilitate seamless document management, automate freight tracking and let you share live order and shipment updates with warehouses and customers.
Preparing for the holiday rush
Scenario planning is the best way to protect your supply chain from the risk that comes with the holiday rush.
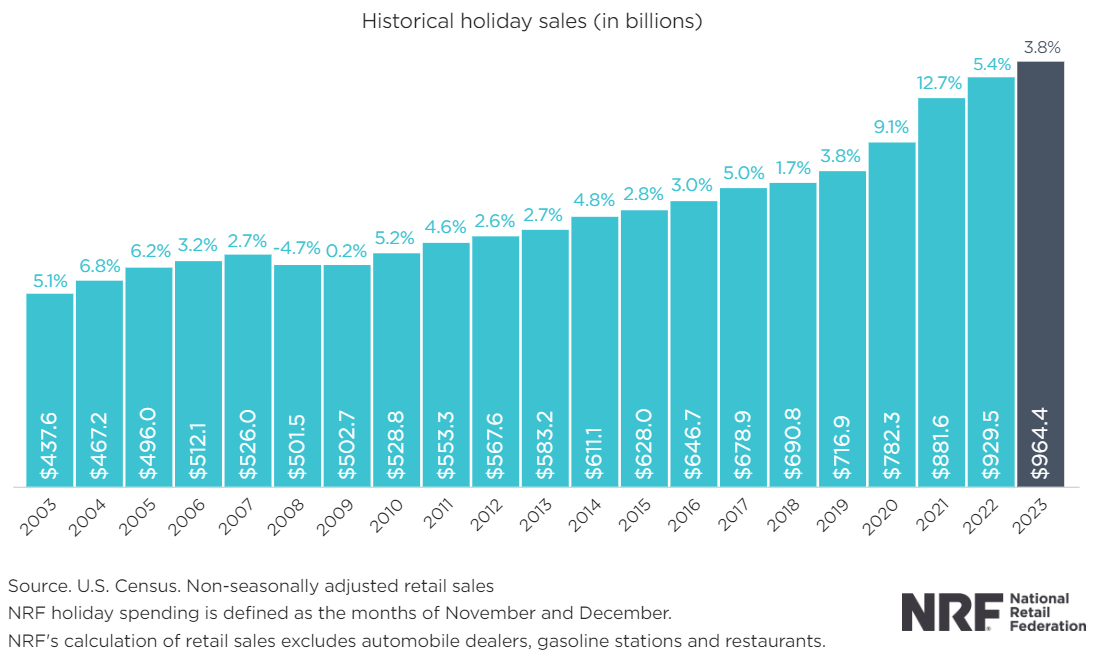
1. Secure space for your containers early
Finding enough carrier capacity at the right price during this period can be a challenge as there are usually peak season surcharges and other delay surcharges during this period which can put pressure on shippers. Shippers should work with carriers and logistics partners to plan ahead and secure capacity contracts to mitigate against these risks.
This can be done by negotiating early with carriers and focusing on space availability (rather than just pricing) to ensure that the space is available on priority.
2. Ensure sufficient warehouse and transport capacity
In addition to vessel capacity, shippers must also consider factors such as warehouse management and delivery networks. During holiday seasons it is common to find that warehouses, fulfillment centers, labor and delivery networks are all stressed due to congestion caused by larger than normal volumes.
This has the potential to create disruptions in inventory operations and have a knock-on impact on customer delivery times as everyone is clamoring for the same space and delivery schedules.
3. Frontload inventory
While carrying excess inventory does come with a cost, it is a form of insurance against the unpredictability that comes with Q4 shipping volumes. For non-perishable and durable goods, plan to bring cargoes in during non-peak periods to avoid the holiday rush. This would be beneficial for vessel space, freight rates and equipment.
4. Develop contingency plans for last-mile delivery
Consumers today expect a variety of options including same day delivery, curbside pickups and alternative delivery locations. To deliver the omnichannel customer experience, shippers must prepare for last-mile delivery complications including urban congestion, traffic, the availability of customers for delivery and a host of other factors that can add pressure on logistics network operations.
Shippers should have a backup plan for last-mile delays including relationships with a range of local couriers or creating micro-fulfilment centers especially in major metros which can make a significant difference in improving operational efficiencies and meeting consumer demands.
Managing the chaos with a visibility platform
While good planning will put you in a strong position to get through the holiday period with minimal disruption, there will inevitably be issues.
Adopting a supply chain visibility platform (like Beacon) will ensure you are alerted to delays and disruptions as soon as they arise. By tracking all your shipments in a single hub, visibility solutions provide a single source of truth and can help you understand where things are in just a few clicks.
Collaborative visibility platforms take things a step further by enabling data sharing, communication and document management across supply chain stakeholders. By giving everyone real-time access to the same information, you can improve transparency, reduce logistics admin and move quicker to mitigate issues as they arise.
Building a holiday shipping playbook
At the end of the season, it’s good practice to do a retrospective analysis (“post mortem”) to understand where things went well, and where they went wrong so you can document lessons learned for next year. These insights can be fed into playbooks that outline best practices for managing the risks associated with the holiday period.
A successful Q4 starts with a good plan
The holiday season poses several unique challenges for retailers, wholesale distributors and the logistics services industry. Through careful planning and proactiveness coupled with advanced technologies, these challenges can be overcome or their impact minimized.
Real-time visibility solutions can help you stay on top of all your orders and shipments amidst the holiday chaos.