ABC Analysis is a method used in supply chain management to categorize inventory into three groups—A, B, and C—based on their importance. This classification helps businesses prioritize their resources and focus on the most critical items.
An Advanced Shipping Notice (ASN), sometimes referred to as Advance Ship Notice, is a notification sent by a supplier or manufacturer to a customer or retailer to provide detailed information about a pending shipment. The ASN serves as an electronic document that outlines the contents of the shipment before it physically arrives at the destination.
An agile supply chain is a flexible and responsive approach to supply chain management that enables organizations to quickly adapt to changing market conditions, customer demands, and disruptions. It focuses on enhancing speed, efficiency, and adaptability throughout the entire supply chain process, from sourcing raw materials to delivering finished products to customers.
An air waybill (AWB) is a vital logistics document used in air freight transportation. It serves as a contract of carriage between the shipper (consignor) and the airline (carrier), detailing the terms and conditions of air transportation for the shipment. The air waybill contains essential information such as the origin and destination of the cargo, the description of goods, the weight, and the freight charges.
An arrival notice is a notification sent by a carrier or freight forwarder to inform consignees or recipients that a shipment has arrived at its destination port or facility. This notice serves as an important communication tool in the supply chain, providing recipients with essential information about the arrival of their goods and detailing the next steps for delivery or pickup.
An Automatic Identification System (AIS) is a tracking system used in the maritime industry to monitor the location and movement of ships. AIS provides real-time information about vessel identification, position, course, and speed.
Backhauling is a transportation logistics practice where trucks carry a return load on their way back from delivering goods to their destination. Instead of returning empty, trucks utilize their empty space to transport goods from the destination back to the point of origin or another destination along the route.
In supply chain management, "backorder" refers to a situation where a customer places an order for a product that is temporarily unavailable in the seller's inventory. When an item is on backorder, it means the customer's order cannot be fulfilled immediately due to insufficient stock levels.
A bay plan is a diagram that details the stowage of containers on a vessel, specifying their exact position by bay, row, and tier to ensure efficient and safe loading and unloading operations.
A Beneficial Cargo Owner (BCO) is the entity with ownership or a beneficial interest in transported goods. While not always the shipper, the BCO reaps the benefits of the cargo's arrival.
A bill of lading (B/L) is a legal document issued by a carrier or its agent to acknowledge receipt of goods for shipment. It serves as a contract between the shipper (seller) and the carrier (transport provider), detailing the terms and conditions of transportation, including the type, quantity, and destination of the goods.
Blank sailing is a term used to describe the situation when a shipping line cancels a scheduled port call or an entire voyage. This can happen for various reasons, such as low demand for shipping services, operational issues, or unforeseen circumstances like bad weather or port congestion.
A blind shipment refers to a logistics practice where certain details about the shipment, such as the sender, receiver, or contents, are intentionally obscured or withheld from one or both parties involved in the transaction. This is typically done to maintain confidentiality or to prevent competitors from obtaining sensitive information about suppliers, customers, or pricing.
A bonded warehouse is a secured facility authorized by customs authorities where imported goods can be stored, manipulated, or undergo manufacturing operations without payment of duty.
A booking confirmation is a document that verifies the reservation of space for cargo on a carrier’s vessel, flight, or truck, ensuring all shipping arrangements are approved and scheduled.
A request for reservation of space and equipment for a particular vessel/voyage and possibly inland transport.
Break bulk cargo refers to goods that are individually packaged or bundled, rather than being transported in containers or in bulk. These items are often large or irregular in size and include products like machinery, vehicles, construction materials, or heavy equipment.
Buffer stock, also known as inventory buffer or stock buffer, refers to the extra inventory held by a company to mitigate the risk of stockouts caused by uncertainties in supply and demand. It acts as a cushion against fluctuations in customer demand, supply chain disruptions, and variations in lead times.
Bulk cargo refers to commodities that are transported unpackaged in large quantities, typically stored and handled in bulk form, rather than in individual units or containers. This category of cargo is crucial in global trade, especially for goods that are homogeneous and not easily damaged during transportation.
The bullwhip effect, also known as demand amplification or whiplash effect, is a phenomenon that occurs in supply chains where small fluctuations in demand at the consumer level lead to exaggerated fluctuations in demand further upstream in the supply chain. This amplification of demand variability causes inefficiencies, such as excess inventory, stockouts, and increased costs, as supply chain partners overreact to perceived demand changes.
CIF, or Cost, Insurance, and Freight, is an international shipping agreement used in the transportation of goods. In freight shipping, CIF means that the seller takes responsibility for the cost of transporting goods to the buyer's destination port. This includes paying for shipping, handling, and insurance. The seller's obligations end when the goods reach the destination port, at which point the buyer assumes responsibility for customs clearance, import duties, and any further transport to their final destination.
A Capesize ship is a large bulk carrier vessel designed to transport heavy raw materials across long distances, too large to transit through canals like the Panama or Suez.
The action of allowing cargo to leave the container yard typically authorized by the carrier. This is often confused with gate-out, but cargo release is the authorization necessary before shipments can be allowed to gate-out.
A cargo survey is an inspection process that assesses the condition and quantity of goods during transportation to ensure compliance with shipping terms and prevent disputes.
A shipping carrier is an organization that provides transportation services for goods. They manage the logistics of moving cargo, which includes loading, transporting, and delivering goods to the specified location. Shipping carriers handle various types of shipments, from small packages to large freight consignments, using different modes of transportation such as maritime, air, rail, and road.
Carrier haulage refers to a transportation arrangement where the carrier, typically the ocean shipping line or its designated transport provider, is responsible for arranging and paying for the inland transportation of containers. In this scenario, the carrier takes charge of moving the container from the port of discharge to the final destination or vice versa, using their own transportation assets or subcontracted carriers.
A carrier scorecard is a performance measurement tool used by supply chain and logistics professionals to evaluate the effectiveness and reliability of their freight carriers. It provides a standardized way to assess carriers based on various performance metrics, helping organizations make informed decisions about their logistics partners
A certificate of origin is a document issued by an authorized body or organization that certifies the country in which the goods being shipped were manufactured, produced, or processed. It serves as a declaration by the exporter to the customs authorities of the importing country, providing information about the origin of the goods and facilitating trade by ensuring compliance with trade agreements, tariffs, and regulations.
A commercial invoice is a crucial document used in international trade transactions to provide details of the goods being shipped and their corresponding value. It serves as a formal request for payment from the buyer to the seller and is essential for customs clearance and regulatory compliance.
In shipping, a commodity refers to bulk goods or raw materials that are transported in large volumes as part of global trade.
In the realm of supply chain and logistics, the term "Consignee" refers to the individual, company, or entity to whom a shipment of goods is delivered. The consignee is the designated recipient or receiver of the goods, typically identified by name and address on shipping documents such as the bill of lading or delivery order.
Consignment inventory is a supply chain arrangement where a supplier (consignor) retains ownership of goods while they are held at a customer's (consignee's) location. The consignee only pays for the goods when they are sold or consumed, and the supplier retains responsibility for managing and replenishing the inventory as needed.
In shipping and logistics, a consignor refers to the entity or person who is the sender or shipper of goods. The consignor is responsible for initiating the shipment of goods from one location to another, typically to a consignee or recipient.
A container depot is a facility used for the storage, maintenance, and repair of empty shipping containers when they are not actively in use for transportation.
Container discharge is the process of unloading shipping containers from a vessel at a port, using cranes and other equipment, for onward transportation.
A container freight station (CFS) is a designated facility where goods are received, sorted, and prepared for onward transportation, enhancing efficiency in logistics operations.
Shipping container grades classify containers based on their condition and suitability for transporting goods, ranging from cargo-worthy to as-is quality.
A container packing certificate is a document that verifies the proper packing and loading of goods into a shipping container. It attests that the contents have been securely packed, arranged, and secured according to industry standards and regulatory requirements. Obtaining a container packing certificate is crucial for compliance with international shipping regulations and contractual obligations. It provides assurance that the goods have been properly prepared for transport, minimizing the risk of delays, damages, or disputes during the shipment process.
A container rollover occurs when a shipping container is not loaded onto its scheduled vessel and is instead 'rolled over' to a subsequent vessel. This delay means the container misses its intended departure and must wait for the next available sailing, which can significantly impact lead times and delivery schedules.
Container stripping (devanning) is the process of unloading cargo from a shipping container at its destination for inspection, storage, or further distribution.
Container stuffing is the process of loading cargo into a shipping container in a safe and space-efficient manner for transportation.
Cross docking is a logistics strategy where incoming goods from suppliers are unloaded from incoming trucks or containers and directly loaded onto outbound trucks or trailers, with minimal or no storage time in between. Essentially, it involves transferring goods directly from the inbound dock to the outbound dock, bypassing the need for traditional warehousing storage.
A customs broker is a licensed professional who specializes in facilitating the clearance of goods through customs barriers for importers and exporters. Acting as intermediaries between businesses and customs authorities, customs brokers ensure compliance with regulations and smooth passage of goods across international borders.
Customs clearance refers to the process of fulfilling the legal requirements necessary to facilitate the import or export of goods across international borders. This procedure ensures that shipments comply with local laws and regulations, allowing them to enter or leave a country legally. It involves various documentation, inspections, and payments of duties and taxes.
A customs manifest lists in detail all the bills of lading issued by a carrier, its agent or master for a specific voyage and port call. It is a detailed summary of the total cargo of a vessel and is used principally for customs purposes. It acts as a declaration to customs authorities, ensuring compliance with regulations and facilitating smooth movement of goods through ports and checkpoints.
The latest point in time where a container has to be delivered to a terminal to be loaded on a vessel, or where certain documentation has to be provided by the Shipper.Example: CY cut-off, FCL cut-off, VGM cut-off, DG cut-off.
Cycle counting is a methodical approach to inventory management where a subset of inventory is counted on a continuous basis, typically throughout the year. Unlike traditional annual or periodic inventory counts that halt operations, cycle counting allows businesses to maintain regular operations while ensuring accurate stock levels.
DAP, or Delivered At Place, is a term used in international trade that specifies the seller's obligation to deliver goods to a designated location in the buyer's country. In DAP terms, the seller is responsible for all costs and risks associated with delivering the goods to the agreed-upon destination. This includes arranging transportation, handling charges, and insurance up to the point of delivery. The buyer, however, is responsible for unloading the goods, handling customs clearance, and paying any import duties and taxes once the goods arrive at the destination.
DDP (Delivered Duty Paid) shipping terms dictate that the seller assumes all responsibilities and costs associated with delivering the goods to the buyer's specified destination. This includes transportation, insurance, handling charges, and import duties and taxes. Essentially, the seller handles everything from the point of origin to the final delivery location, ensuring the goods arrive ready for use by the buyer without any additional costs or logistical burdens.
DDU, or Delivered Duty Unpaid, is an international shipping term that defines the responsibilities of the seller and buyer. Under DDU terms, the seller delivers the goods to a specified destination in the buyer's country, covering all costs and risks associated with transportation, except for duties, taxes, and other import charges which are the responsibility of the buyer. The seller's obligations include arranging and paying for freight, insurance, and handling charges until the goods reach the agreed-upon place.
DPU, or Delivered at Place Unloaded, is a term used in international trade that specifies the seller's responsibility to deliver and unload goods at a designated location in the buyer's country. Under DPU terms, the seller bears all costs and risks associated with transporting and unloading the goods at the agreed destination. This includes all transportation costs, including freight, insurance, and handling charges, up to and including the unloading of the goods at the destination. The buyer then takes over responsibility for import duties, taxes, customs clearance, and any further transport to the final destination.
A dangerous goods declaration (DGD) is a legal document required for the transportation of hazardous materials or dangerous goods by air, sea, road, or rail. It provides detailed information about the nature, classification, packaging, and handling requirements of the dangerous goods being transported. The DGD helps ensure compliance with international regulations and facilitates the safe handling and transport of hazardous materials throughout the supply chain.
Deadheading is the practice of operating a commercial vehicle, such as a truck or a trailer, without any cargo or paying passengers. Essentially, it refers to the movement of a vehicle while it is empty, either on its way to pick up a load or after delivering a load to its destination.
Deadweight tonnage (DWT) is a measure of a ship's carrying capacity, representing the total weight of cargo, fuel, crew, provisions, and other materials that the vessel can safely carry.
Demurrage refers to the additional charges imposed on the owner or operator of a vessel, freight car, or truck for delaying the use of equipment or facilities beyond the agreed-upon time. In the context of maritime shipping, demurrage applies to the time that cargo remains at the port or terminal beyond the allotted free time for loading or unloading.
Detention charges are fees incurred when a carrier's equipment, such as containers or trailers, is held beyond the agreed-upon free time at a facility, such as a port, terminal, or warehouse. These charges compensate the carrier for the additional time their equipment is detained and unavailable for other use.
A supply chain digital twin replicates the entire supply chain network, including assets, facilities, products, and processes, in a digital environment. It enables real-time monitoring, analysis, and simulation of supply chain operations to improve efficiency, optimize decision-making, and mitigate risks.
Dimensional weight, also known as volumetric weight, is a pricing technique used by shipping carriers to calculate the cost of shipping packages based on their volume rather than just their actual weight. This method helps carriers account for the space that a package occupies in relation to its weight, ensuring fair pricing for shipping services.
A dock receipt is a logistics document issued by a carrier or its agent to acknowledge the receipt of goods at a shipping dock or terminal for transportation. It serves as a temporary receipt until the goods are loaded onto a vessel or other mode of transportation for shipment to their destination. The dock receipt contains essential information about the cargo, such as the quantity, description, condition, and destination, along with details about the carrier, shipper, and consignee.
A ship’s draft (draught) measures the depth of the vessel below the waterline, which determines the minimum water depth required for safe navigation.
Drayage refers to the transportation of goods over a short distance, typically within the same metropolitan area or between nearby facilities. It plays a crucial role in the logistics and supply chain industry, linking various points in the transportation network, such as ports, rail terminals, and distribution centers. Drayage often involves moving goods from a transportation hub like a port to a nearby warehouse or vice versa.
Drop shipping is a retail fulfillment method where a store doesn’t keep the products it sells in stock. Instead, when a store sells a product using the drop shipping model, it purchases the item from a third party and has it shipped directly to the customer.
Dry bulk cargo refers to unpackaged, loose commodities that are shipped in large quantities and typically consist of raw materials. These goods are usually loaded directly into the holds of a vessel without any packaging, making them different from containerized or break bulk cargo.
A booking received via Electronic Data Interchange, a standard electronic format for exchanging business documents within the supply chain, such as purchase orders, invoices, shipping notices, and other transactional information.
An Economic Operators Registration and Identification (EORI) number is a unique identifier assigned to businesses engaged in international trade within the European Union (EU) and certain other countries. It serves as a means of tracking and identifying entities involved in import, export, and other customs-related activities.
In shipping, ETA refers to the anticipated arrival time of a vessel, truck, or aircraft at a specified port or delivery location. It is calculated based on various factors such as the departure time, transit duration, and any potential delays due to weather, customs, or other unforeseen circumstances. This prediction helps logistics professionals plan and coordinate the movement of goods, ensuring timely deliveries and efficient supply chain management.
EXW, or Ex Works, is one of the Incoterms (International Commercial Terms) published by the International Chamber of Commerce (ICC). It defines the responsibilities of buyers and sellers in international transactions. Under EXW terms, the seller fulfills their obligation by making the goods available for pickup at their premises (factory, warehouse, etc.). The buyer assumes all risks and costs associated with transporting the goods from the seller’s location to the final destination.
Economic Order Quantity (EOQ) is a fundamental concept in inventory management that determines the optimal quantity of goods a company should order to minimize total inventory costs. It balances the costs of holding inventory (holding costs) and the costs of ordering inventory (ordering costs) to find the most cost-effective quantity to order at any given time.
An Electronic Product Code (EPC) is a unique identifier used to distinguish individual items, cases, or pallets in the supply chain. It serves as a digital identifier that provides a standardized way to track and manage products throughout their lifecycle, from manufacturing to distribution to retail.
Used for storing cargo in/on during transport. The equipment "size/type" is defined by the ISO 6346 code. The most common equipment size/type is 20'/40'/45' Dry Freight Container, but a number of different versions exist.
Confirmation & receipt of the equipment loaded/discharged on a vessel during a port call. This information is recorded by the terminal operator and sent to the carrier. This is often done using the EDI message - COARRI. The COARRI message reports that the equipment specified have been discharged from a seagoing vessel (discharged as ordered, over landed or short landed), or have been loaded into a seagoing vessel.
A shipping exception is an unexpected event or disruption that causes a shipment to deviate from its planned delivery schedule.
Expedited freight refers to a specialized service in logistics and supply chain management aimed at transporting goods quickly and efficiently to meet tight delivery deadlines. It is used when standard shipping methods cannot meet the required delivery timeframe, typically due to urgent customer needs, production delays, or unforeseen circumstances.
FAS, or Free Alongside Ship, is a shipping term used in international trade that specifies the seller's responsibilities and costs up to the point where goods are placed alongside the buyer's vessel at the designated port of shipment. The buyer then assumes all risks and costs from that point forward.
FCA, or Free Carrier, is an Incoterm (International Commercial Term) used in international trade to define the point at which the seller's obligations are fulfilled and the buyer assumes responsibility for the goods. Under FCA, the seller delivers the goods, cleared for export, to the carrier or another party nominated by the buyer at a specified place.
FCL (Full Container Load) freight involves shipping an entire container for a single shipper, offering faster and more secure transport, especially for large-volume cargo.
FOB, or Free on Board, is a term used in international trade to indicate when ownership and liability for goods transfer from the seller to the buyer. It specifies the point at which the seller is no longer responsible for the goods. This term is crucial for determining who pays for shipping, insurance, and other logistics costs, as well as who bears the risk during transit.
An entity operating a feeder service - ref. Feeder vessel.
A container feeder vessel, also known as a feeder ship, is a relatively small cargo vessel that is specifically designed for transporting containers between smaller ports or terminals to larger hub ports where mainline vessels operate. These vessels serve as a crucial link in the global shipping network by facilitating the distribution of cargo to and from regional ports that may not be accessible to larger ships due to navigational constraints or limited infrastructure.
A Feedermax container ship is a medium-sized vessel used to transport containers between regional ports and major ports, connecting smaller markets to global shipping routes.
Fill rate in supply chain management refers to the measurement of how fully customer demand for a product or service is met through the availability of inventory. It indicates the percentage of customer orders or demand that can be fulfilled immediately from stock, without backorders or delays.
A "Flag of Convenience" (FOC) refers to the practice of a ship's owner registering a merchant vessel in a country other than the owner’s country of origin to benefit from more favorable regulations, often related to taxes, labor laws, and safety standards. This practice allows shipowners to operate under less stringent regulations, often reducing operational costs and increasing profitability. However, FOC can also lead to concerns about safety, environmental standards, and working conditions for crew members, as the regulatory oversight in these flag states might not be as rigorous.
4PL, or Fourth Party Logistics, refers to a logistics model where a single organization, known as the fourth-party logistics provider, takes on the responsibility of managing and coordinating the entire supply chain on behalf of the client. Unlike traditional third-party logistics (3PL) providers, who primarily handle specific logistics functions, 4PL providers offer comprehensive end-to-end supply chain management services. 4PL providers act as strategic partners, overseeing multiple 3PLs and other service providers to optimize supply chain operations, enhance efficiency, and achieve cost savings for their clients.
A free trade zone (FTZ) is a designated area within a country where goods can be imported, stored, manufactured, or exported without being subject to the usual customs duties and tariffs.
A freight forwarder is a vital link in the supply chain, specializing in the coordination and management of international shipments. Acting as an intermediary between shippers and carriers, freight forwarders handle various logistics tasks such as booking cargo space, arranging transportation, preparing documentation, and managing customs clearance.
Freight visibility (also called shipment visibility) refers to the ability of supply chain professionals to track and monitor the movement of freight shipments throughout the supply chain. It involves gaining real-time insights into the location and status of goods as they move through various transportation modes and stages of the logistics process.
Full truckload (FTL) freight refers to shipments that occupy the entire capacity of a truck trailer. Unlike less than truckload (LTL) shipments, FTL shipments do not share space with other cargo, allowing for direct transportation from the point of origin to the destination without intermediate stops.
The GLEC (Global Logistics Emissions Council) framework is a globally recognized standard developed to measure and report greenhouse gas (GHG) emissions from logistics activities. It provides guidelines and best practices for calculating emissions across various modes of transport, including road, rail, sea, and air.
The action of moving a container from a container yard, a terminal or another restricted/controlled area.
The German Supply Chain Act, also known as Lieferkettengesetz, is a landmark legislation enacted to promote corporate social responsibility and ensure ethical practices throughout global supply chains. Introduced in 2021, the law applies to German companies with over 3,000 employees, requiring them to monitor and address human rights abuses, environmental violations, and labor standards in their supply chains.
A Global Trade Item Number (GTIN) is a unique identifier assigned to products in the supply chain to facilitate efficient tracking and management from production to point of sale. It provides a standardized method for identifying items globally, ensuring accurate inventory control, and enabling seamless transactions between trading partners.
A Goods Receipt Note (GRN) is a document used in the process of confirming the receipt of goods from a supplier or vendor. It serves as an acknowledgment by the receiving party, typically a warehouse or a buyer, that the goods specified in the accompanying purchase order have been received in satisfactory condition.
Green logistics refers to the process of minimizing the environmental impact of logistics and supply chain activities, including transportation, warehousing, packaging, and distribution.
A Handysize ship is a small to medium-sized bulk carrier designed for transporting various cargo types, capable of navigating smaller ports and shallow waters.
Gear used to do inland transportation of a container. This can include tools and apparatus used to load/discharge the container onto the intermodal type.
Specifications for a haulier set by a carrier in regards to a specific work order, e.g. timeline, capabilities.
The joint term for merchant and carrier haulage. It should be noted that a shipment can have several types of haulage throughout the transport from origin to destination.
A haulier, also known as a trucking company or a carrier, is a business or individual that transports goods by road using trucks or lorries. Hauliers play a vital role in the transportation industry, moving goods between locations such as warehouses, distribution centers, manufacturing facilities, ports, and retail stores.
A House Bill of Lading (HBL) is a transportation document issued by a freight forwarder or Non-Vessel Operating Common Carrier (NVOCC) to acknowledge receipt of goods for shipment. It serves as a contract of carriage between the shipper and the carrier and includes details such as the type, quantity, and destination of the goods being transported.
In supply chain logistics, a hub and spoke model refers to a system where goods or services are transported through a central hub to various spoke locations. The hub acts as a central point for collection, sorting, and distribution, while the spokes represent the routes connecting the hub to different destinations.
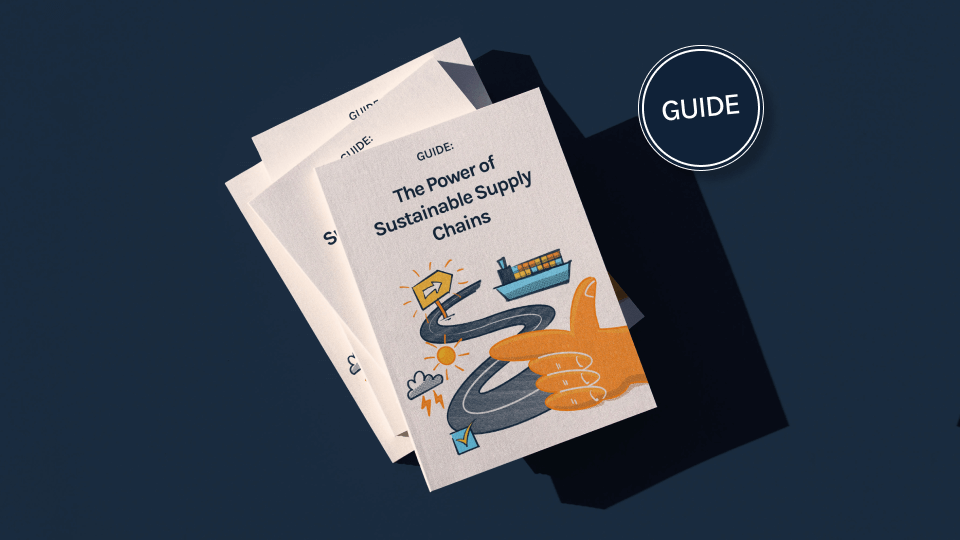
The power of sustainable supply chains: Everything you need to know to take action and lead the way
None of us work alone. We’re all part of global supply chains that stretch from Shanghai to Sheffield and from Sydney to San Francisco. And that’s why it’s so important for everyone involved in manufacturing, shipping, and distribution to play their part in making their segment of those supply chains as sustainable and environmentally responsible as possible.
It’s no small task though. Even the most switched-on and visibly sustainable companies out there have plenty of work to do – because cleaning up direct carbon emissions is just a drop in the ocean compared to tackling the indirect emissions from your supply chain.
In fact, a large-scale McKinsey study in 2016 found that “the typical consumer company’s supply chain creates far greater social and environmental costs than its own operations, accounting for more than 80 percent of greenhouse-gas emissions and more than 90 percent of the impact on air, land, water, biodiversity, and geological resources.”
So although many companies have switched to renewable energy and other sustainable ways of operating within their premises, the overall effects of their operations may not have changed very much at all.
Luckily, it’s not all doom and gloom. Companies are taking responsibility for their supply chains. Cleaning them up and making systematic changes to keep them that way.
New sustainable supply chain management technology is helping by making it easier to track, report and reduce your carbon footprint. There’s never been a better time to make the adjustments that will change our world for the better.
Sustainable supply chains are no longer optional
While we all like to think companies do the right things for the right reasons, there are still costs associated with driving sustainability in supply chains. In the past, that might have meant it would fall down a company’s list of priorities – and that’s totally understandable. Deciding between an investment in sustainability and something else like opening a new factory or expanding into a different region is never an easy choice.
A few years ago, a lot of companies may have gravitated towards the latter options. But that’s changing. Ernst & Young’s 2022 survey of supply chain leaders reveals that “visibility throughout the supply chain is the top priority for supply chain executives”, up from second place in the two years before.
This is partly because there are cost-saving and revenue growth benefits to more efficient supply chain management. But another common theme from the survey is that supply chain visibility is becoming a much greater priority as businesses face added pressure from customers, employees, and government regulators. Particularly when it comes to carbon emissions, sustainable sourcing, and labor conditions.
Who is demanding more sustainable supply chains?
In the court of public opinion, sustainability has never mattered more. If a company isn’t seen to be taking appropriate steps, there’s a real risk that its customers might take their business to a more responsible partner.
That same Ernst & Young survey shows that pressure from customers is the fifth-strongest motivator for improving supply chain sustainability, with higher expectations from employees sitting just behind it.
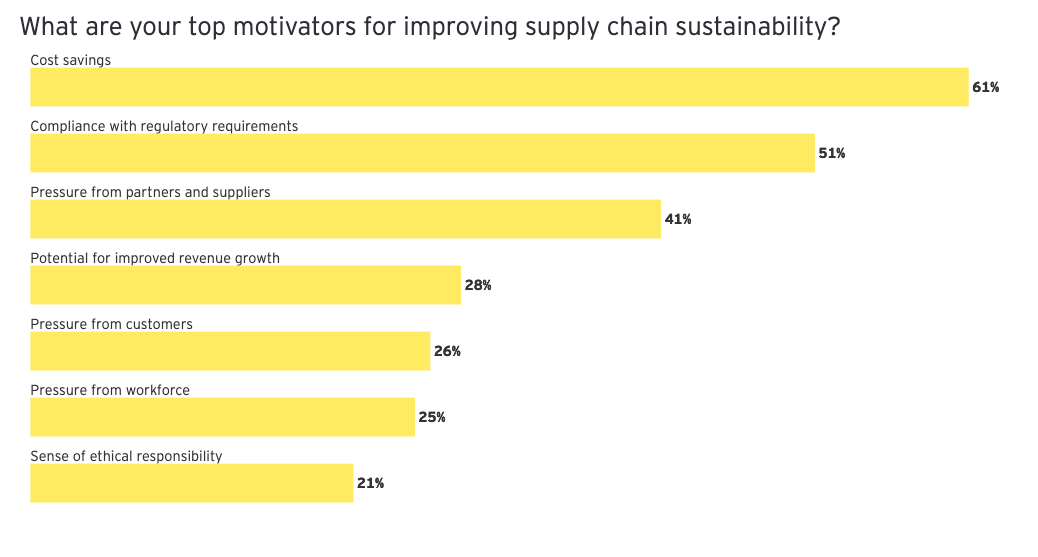
Input from partners and suppliers also plays a part. But aside from the potential savings that are always going to be the biggest driver of change, the dominant influencing factor is new regulations that are forcing the hands of even the most resistant companies.
For example, the EU is in the process of introducing new sustainability standards that require companies to audit their full global supply chains including every single one of their direct and indirect relationships. The goal of this is to make sure organizations in the EU are fully compliant with not only environmental protocols, but human rights and governance standards too.
Similar regulations are either in place, in progress, or being discussed all over the world. It’s only a matter of time before they become the norm, so the conversation is now a matter of ‘when’, not ‘if’, the evolution happens.
Plus, the more companies that prioritize sustainability in supply chains, the easier it becomes for others to follow in their footsteps – taking advantage of the new tech and ways of working that the leaders are pioneering.
That’s the knock-on effect at play. Once enough of us decide to make a change, the people we work with will be empowered and incentivized to do the same.
To get there though, we all need a thorough understanding of what sustainable supply chains are, and the tools that can be leveraged make them a reality.
What is supply chain sustainability?
You might think sustainability is solely about the environment. That’s obviously a huge part of it, but for anything to be truly sustainable, there’s a lot more that has to happen at every step along the way.
In supply chains, sustainability is broken down into three core focus areas: environmental, social, and governance.
This is ESG, and nothing new to most of us. But it’s worth recapping how those three pieces of the puzzle work together in relation to a supply chain.
Environmental supply chain sustainability
It’s impossible to underplay the environmental importance of sustainability in supply chains. That’s because the consequences are some of the most severe – ranging from toxic waste leaks and water pollution to deforestation and long-term damage to the ecosystems our planet relies on to thrive.
To avoid these, there are a lot of different pieces of the supply chain to consider. It’s not just about reducing emissions – although that’s vital.
You’ll need to think about the materials used along the way (like plastic or anything else that’s potentially hazardous to the environment). You’ll also need to work out whether your supply chain is wasting or polluting water – and even if it’s contributing to a loss of biodiversity indirectly through deforestation.
That’s a lot to keep track of, which is why better supply chain visibility is vital. The more you can see and measure, the more you can change and improve. With the right data at your fingertips, you can start benchmarking performance and looking for ways to make a difference.
Social supply chain sustainability
Supply chains are about people too. If every single piece of the process is working in an environmentally friendly way, that’s not worth very much if workers’ health, safety, or human rights are being compromised.
That’s what the ‘S’ in ESG stands for – social. And it means taking ownership of the effects our supply chains have on the lives of everyone involved with or affected by them.
Some of these responsibilities are obvious, like maintaining the very best labor and human rights standards, along with appropriate health and safety measures. But others are slightly more complicated, like ensuring everybody in your supply chain is getting fair pay, and working in environments that support diversity, equity, and inclusion.
Responsible partners will care just as much about these things as you do. So when you start having conversations with suppliers about the importance of sustainability in your shared supply chains, make sure how people are treated is front and center.
Governance supply chain sustainability
Governance is an umbrella term for the way that organizations are managed and run. In supply chains, it refers to all the different rules, regulations, systems, and structures to follow as best practices.
That means having proper risk management tools in place to protect your partners, avoid corruption and bribery, and stick to whatever codes of conduct your organization is obligated to follow. It also means prioritizing transparency, and regularly reporting on different areas of your operations so that partners and customers can see the proof behind your claims about sustainability.
These are all things that you should be expecting your partners to do. If you’re not sure whether they’re following the rules, then it might be time to have a conversation or start rethinking those relationships.
When ESG is a priority, sustainability follows
For a supply chain to be truly sustainable, every person and company involved has to be doing their bit at an environmental, social, and governance level. It can be a lot to manage. But when it happens, supply chains do a lot better for people and the planet.
Even though there are all sorts of factors involved, a lot of them are intertwined and interrelated. A company following a clear code of conduct and managing risk sustainably is going to naturally treat employees better and look for ways to reduce its environmental impact. Just like how making sure a manufacturing process isn’t polluting waterways will have a positive effect on the data you collect – incentivizing greater transparency in reporting.
Little by little, ESG flows through the full supply chain, ultimately making every stage more cost-effective and more sustainable.
Best practices for supply chain sustainability – step by step
Because the ESG elements of supply chains are so interwoven, it doesn’t always make sense to use them as a starting point for your sustainability plan. Instead, it’s often easier to simply break the full supply chain down into different chunks, and then target those specific areas.
So let’s take a look at the key segments of a supply chain and how you can drive sustainability in each of them.
Procurement and purchasing
Before any supply chain can start moving, you’ll need something to move. That’s the procurement stage, when you’ll source the products, materials, or services you need to get things up and running.
Traditionally, companies with a focus on sustainability in supply chains might have focused less on procurement and more on transportation or warehousing. But a recent survey from the Institute for Supply Management shows a growing emphasis on this first step, with leaders from all sectors realizing that better purchasing practices can “create a long-term competitive advantage for their company."
So what does that look like? Well, it all starts with better, more responsible resourcing and stringent vetting before deciding to work with a particular partner. That might include audits, checking qualifications and certifications, or providing incentives that relate to sustainability performance.
But this isn’t just about onboarding new partners. Sustainable companies should also take stock of their existing procurement network, and apply all the same strategies to make sure a long-term partner isn’t compromising your overall supply chain.
Transportation and shipping
We all know that transportation is the foundation of a supply chain.
It’s also one of the most challenging areas of sustainability to address, with air, sea and land transportation making up 15% of greenhouse gas emissions globally.
This is a major focus area at the international regulatory level, so it’s no surprise that almost all supply chain transport providers are investigating and investing in alternate ways of doing things. Those range from investing in alternative fuels all the way through to more energy-efficient ship designs, and the knock-on benefits can be a real boost to your supply chain sustainability.
That gives you options, making it easier to pick and choose providers who are prioritizing sustainability – but only if you’ve got the right information to make those decisions with.
Beacon’s carbon tracking tools are a great place to start, empowering cleaner, greener shipping by making it easy for you to see the full picture of any emissions associated with your shipping.
Once you’ve got that, the ways you reduce your impact are up to you. More strategic route and partner planning is one option, choosing transport companies that use renewable energy or take various steps to limit pollutants. But you can also look at balancing your emissions with carbon offsetting for true net zero. Beacon lets you do that too, thanks to industry-leading offsetting tools powered by our partnership with Lune.
Storage and warehousing
No matter what your supply chain is moving, you’ll need somewhere to keep it. Storage is one of the areas of the supply chain that you might have more control over if it happens on premises that you manage directly. And that makes it a clear opportunity for improved sustainability.
Investing in warehouse fit-outs that reduce their carbon footprints should be your first step. BREEAM’s third-party certified standards are the benchmark for sustainable built environments, and using those standards as a guide can help you reduce your carbon footprint and increase operational efficiency – meaning you’ll save money on running costs too. The standards cover everything from water and energy use to pollutants and waste disposal, so work your way through the list and make sure your facilities are reaching as high a level as possible.
You can also invest in non-building factors like electric fleets and multi-use forklifts, which lower your carbon footprint further. Alternatively, optimized warehouse storage systems make it possible to reduce inventory and minimize the amount of product that’s shifted around unnecessarily.
Ensuring the right health and safety measures are in place is just as important as the environmental side of things, to make sure your sustainability efforts are improving and protecting the lives of team members as well as the world around them.
Of course, a lot of us store goods and products off-site, but all the same steps apply. You’ll just need to spend a bit more time in discussions with your warehousing partner to make sure they’re pulling out all the same stops that you would in their position.
Technology
While technology isn’t an area that necessarily hurts sustainability, it can create enormous potential for positive change.
More and more companies are making the move to renewable energy in their warehouses, plants, and offices – installing solar panels that reduce their carbon impact and limit reliance on fluctuating energy prices.
The benefits of technology are also visible in new types of supply chain sustainability software, which work to make every part of the process more visible, and therefore easier to optimize for ESG. But the benefits don’t stop there. New tech like Beacon is also disrupting the ways that companies track, plan, and report – empowering people at every stage of the supply chain with richer data and the insights they need to improve.
Packaging
Sustainability is nothing new in packaging. These days, we’re all familiar with recyclable materials and circular manufacturing processes that produce less waste and make what we produce easier to get rid of safely.
But there’s always room to do more. With increased levels of online shopping driving more paper, cardboard, and plastic packaging than ever, it’s an area of the supply chain that can always be improved.
Cutting out as much plastic as possible helps, as it is more pollutive and harder to recycle than other alternatives. But you can go a step beyond by exploring fully recycled packaging, or introducing plant-based materials made from natural, biodegradable sources like sugarcane or cornstarch.
From carbon-neutral cartons to sachets made of seaweed, those products are out there, and making the switch is a simple way to instantly and significantly cut down waste.
You may also want to run a packaging audit and rethink your designs entirely – looking for ways to do more with less by reducing weight and size, or eliminating unnecessary elements or purely cosmetic layers. The trade-off you get in looks is easily outweighed by the positive benefits you’ll be able to shout about to your customers and partners.
Reverse logistics
Supply chains usually focus on getting something, somewhere. But what about getting it back? Reverse logistics are a bigger part of our industry than ever, with higher volumes of online shopping naturally leading to knock-on higher returns levels.
What you do with those returns can have a critical impact on sustainability. So look for ways to innovate by repurposing and recycling returned or faulty goods – or by refurbishing and reselling.
You can go further by offering to take back products that have already been used and turn them into something new. That’s already happening in certain sectors like clothing, and it’s a great way for forward-thinking companies to gain an edge both on future production costs and in the minds of their customers.
If any of your materials are perishable, look for ways to shift expiring product earlier, or to safely dispose of it on-site rather than sending it to landfill. There may be up-front costs linked to introducing these sorts of processes, but over time the savings will add up. Plus, you’ll be able to rest easy knowing you’re already a few steps ahead of whatever regulations around waste may come in the future.
How else can you make your supply chain more sustainable?
Even if you’re following all the best practices for supply chain sustainability, there are still plenty of other ways to keep yourself ahead on the road to responsibility.
Set clear, realistic objectives and measure your progress
You won’t be able to make a lasting change if you don’t have the historical information and regular benchmarking to see where you’re making progress. That’s where data comes in, giving you a clear, up-to-date picture of your overall supply chain sustainability and any areas within it where there’s still work to do.
Your first step should always be a thorough audit of your full supply chain using dedicated sustainable supply chain management tools like Beacon, which you can then build into specific targets and goals. Those might be based on what your competitors are doing, or you may want to sign up for a certain target through a program like the Science Based Targets initiative.
Whatever goal makes the most sense, once you’ve got it, you’ll need to make sure you know how close you are to achieving it. That’s another area where software helps, giving you real-time insight into how your adjustments are adding up to real change.
Engage and communicate with partners and customers
Last but not least, lasting sustainability means taking all of the information you have and the progress you’ve made and making it accessible to others. That could be through direct conversations, or publishing regular, transparent reports that show your journey from A to B – and the steps you took to get there.
Some of your supply chain partners might not be as aware of the ways they can improve their performance. But by sharing your expertise, you can help them implement similar checks and balances into their own operations.
That’s nothing but good news for you as part of their supply chains, because the benefits really do flow both ways – giving everyone in your supply chain sustainability performance to be proud of.
Plus, transparency is something your end-customers will value just as much as your partners. Nobody wants to be accused of greenwashing – talking the talk about sustainability without backing it up with tangible change.
But if you can show that you’re making a concerted effort to do better at environmental, social, and governance levels, your customers will know that continuing to choose you is a responsible option for the long term.
Make sustainability a priority and lead the way in your supply chain
There are hundreds of different ways to prioritize sustainability. But it’s only by embedding it into your organization from the top down that you’ll be able to take all the steps needed to become a leader rather than a follower.
That’s what’ll keep you ahead of the regulations that are only going to become stricter as time goes on, while helping you stand out and stand prouder in a market where morals matter more than ever.
There’s no better time than right now to put a plan in place that makes your supply chain a more sustainable one.
Following all the steps in this guide will give you the right foundations, and investing in cutting-edge technology means you’ll be ready to build on them. So start measuring your carbon footprint today and making your supply chain more sustainable for tomorrow.